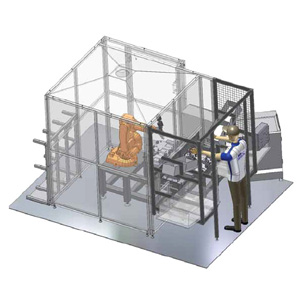
Realizacja dla Delphi Poland S.A.
Automatyzacja procesów produkcyjnych z wykorzystaniem robotów przemysłowych, często w opinii klientów wiąże się z dużymi nakładami finansowymi. Stąd, przy realizacji tego typu zadań, szczególną uwagę należy zwrócić na to aby maksymalnie wykorzystać możliwości jakie drzemią w układach sterowania robotów i niepotrzebnie nie przepłacać za zbyt skomplikowane systemy.
Przemyślany projekt
Przykładem podejścia zakładającego wykonanie zrobotyzowanej aplikacji, optymalnie dopasowanej do wymagań funkcjonalnych, jest stanowisko zrealizowane przez firmę Pro-Zap Sp. z o.o. dla Delphi Poland S.A. oddział Ostrów Wielkopolski.
Klient zwrócił się do firmy Pro-Zap o zaprojektowanie i wykonanie stanowiska spawania elementów kondensorów: zbiorników i wsporników. Warunki, które postawiono to oczywiście – poza wysoką jakością i powtarzalnością procesu – krótki czas cyklu, prostota obsługi, elastyczność, mobilność stanowiska i akceptowalna cena. Po analizie, zdecydowano się na realizację postawionego zadania przez wykorzystanie robota IRB 140 firmy ABB współpracującego ze źródłem spawalniczym firmy Fronius.
Standardowe stanowiska zrobotyzowane wykorzystują robota do realizacji samego procesu technologicznego, a nadzór nad całym stanowiskiem tj. obsługa przycisków, lampek, układów bezpieczeństwa, dodatkowych napędów, komunikację z operatorem, przejmuje sterownik PLC połączony z panelem operatorskim.
W projektowaniu omawianej aplikacji, zrezygnowano ze sterownika PLC i panelu operatorskiego, a ich zadanie przejął robot. Komunikacja z operatorem (wyświetlanie komunikatów diagnostycznych, parametryzowanie procesu, obsługa poszczególnych elementów w trybie ręcznym) odbywa się za pośrednictwem pulpitu z przyciskami i przede wszystkim panelu programowania robota. Zadania zwykle realizowane przez sterownik PLC, przejęte zostały przez układ sterowania robota wyposażony w tym celu w opcję wielozadaniowości (w wypadku robotów firmy ABB opcja dodatkowa tzw. multitasking, niewystępująca w standardowej wersji systemu).
Robot, poprzez interfejs komunikacyjny DeviceNet, współpracuje ze źródłem spawalniczym, a w skład stanowiska wchodzi jeszcze stół obrotowy, na którym zamontowane zostało odpowiednie oprzyrządowanie z pneumatycznymi dociskami. Obszar pracy robota zabudowany został w taki sposób, aby dostęp do niego był możliwy po otwarciu drzwi chronionych zamkiem elektromagnetycznym. Operator ma w normalnym trybie pracy dostęp tylko do obszaru załadunku i rozładunku detali, który to obszar chroniony jest przez bariery bezpieczeństwa.
Zrobotyzowane spawanie
Praca stanowiska przebiega w następujący sposób: operator układa elementy w gniazdach rozmieszczonych po jednej stronie stołu obrotowego (po wcześniejszym rozładowaniu tych, które wykonane zostały w poprzednim cyklu); po zakończeniu załadunku wycofuje się z obszaru chronionego barierami, potwierdza to odpowiednim przyciskiem, co z kolei aktywuje pneumatyczne dociski. W tym samym czasie robot spawa elementy umieszczone w gniazdach na drugiej stronie stołu obrotowego. Po zrealizowaniu operacji na obydwu stronach stołu, następuje automatyczny obrót i cykl może rozpocząć się od nowa. Ponieważ rozładunek gotowych detali i załadunek nowych części odbywa się jednocześnie z pracą robota, cykl pracy zależy niemal tylko od czasu spawania – czas obrotu stołu i czasy przejazdu palnika między kolejnymi spoinami są nieporównywalnie krótsze.
W trakcie pracy automatycznej, na panelu programowania robota wyświetlane są odpowiednie komunikaty dla operatora ułatwiające mu pracę, a w wypadku wystąpienia jakiegoś błędu lub zacięcia, pojawiają się odpowiednie komunikaty diagnostyczne.
W tym miejscu należy podkreślić, że producenci robota i systemu spawalniczego zmodyfikowali zgodnie z projektem swoje produkty tak, aby diagnozowanie ewentualnych problemów związanych z samym procesem spawania, również było maksymalnie uproszczone i możliwe bezpośrednio z panelu programowania robota.
Przełączenie robota z trybu automatycznego do trybu ręcznego powoduje, że na panelu robota wyświetlane jest menu z opcjami, przy pomocy których operator może włączać i wyłączać poszczególne gniazda i tym samym decydować o rodzaju aktualnej produkcji, sterować pojedynczymi dociskami, ustawiać stół obrotowy w określonej pozycji, a także doprowadzać robota w określone położenie: do pozycji wyjściowej; do pozycji kalibracji lub do pozycji, w której możliwe jest sprawdzenie i ewentualne korygowanie położenia elektrody spawalniczej.
Wielozadaniowość i łatwość obsługi
Przy tworzeniu stanowiska starano się maksymalnie uprościć jego obsługę tak, aby nawet operatorom, którzy pierwszy raz stykają się z robotami nie nastręczało to trudności. Dlatego też, rozruch (załączanie układu bezpieczeństwa, załączanie napędów robota, startowanie realizacji programu) sprowadza się do przyciśnięcia kilku przycisków umieszczonych na specjalnie przygotowanym pulpicie i nie wymaga sięgania do panelu programowania robota. Również w trakcie pracy automatycznej, obsługa sprowadza się do rozładunku gotowych części, załadowania nowych i potwierdzeniu przez operatora swojej gotowości jednym przyciskiem.
Jak już wcześniej wspominałem, zadania zwykle realizowane przez sterownik PLC, zostały w tym przypadku przejęte przez robota. Główne zadanie (TASK 0) sekwencyjnie realizuje program pracy robota – przeprowadza końcówkę spawalniczą przez kolejne zadane punkty, sprawdzając po drodze warunki przejścia między nimi oraz załączając i wyłączając źródło spawalnicze w odpowiednich momentach. Należy w tym miejscu zaznaczyć, że tworząc program spawania, dla każdej spoiny można ustawić inne parametry. Część tych parametrów można ustawić bezpośrednio w programie – na przykład prędkość przejazdu. Z kolei typowo spawalnicze parametry dostępne są w sterowniku spawarki w postaci zestawów (tzw. job-ów). Z poziomu programu robota, dla każdej spoiny można wywołać odrębny program w spawarce (dostępne do 100 programów). Proces spawania można również podzielić na trzy fazy: faza zajarzenia łuku, faza spawania zasadniczego, faza wypełniania krateru. Co więcej, dla każdej z faz można zdefiniować odrębne programy spawania. Dzięki temu, możemy mieć 100% kontroli w każdym momencie procesu spawania, a doświadczeni spawalnicy klienta mogą stroić system pod swoje potrzeby z poziomu interfejsu źródła spawalniczego, a więc poziomu dobrze im znanego – bez konieczności zapoznawania się ze specyfiką programowania robota. Oprócz głównego zadania, które może być zatrzymywane (między innymi w wyniku wystąpienia jakiegoś błędu) lub uruchamiane przez operatora, układ sterowania realizuje zadania współbieżne pracujące niezależnie od tego czy zadanie główne jest w danym momencie aktywne czy nie. Te zadania odpowiedzialne są kolejno: za obsługę stołu obrotowego (TASK 1), obsługę przycisków i lampek pulpitu (TASK 2) oraz zamykanie i otwieranie pneumatycznych docisków (TASK 3).
Istotną z punktu widzenia użytkownika, jest także specjalna konstrukcja mechaniczna całego stanowiska. Umożliwia ona bowiem łatwy demontaż stanowiska i ustawienie go w innym miejscu, a po podłączeniu mediów – zasilania elektrycznego i sprężonego powietrza – natychmiastową gotowość do pracy.
Przede wszystkim bezpieczeństwo
W trakcie projektowania i wykonywania stanowiska, założone i spełnione zostały wszelkie normy bezpieczeństwa. W trybie automatycznym, obszar pracy robota nie jest dostępny dla operatora, a obszar pracy stołu obrotowego i strefa działania docisków pneumatycznych chroniona jest przez bariery bezpieczeństwa odpowiedniej kategorii. Dodatkowo, operator ma w zasięgu działania przycisk zatrzymania awaryjnego. W trybie ręcznym, a więc w trybie, w którym można między innymi dokonać modyfikacji trajektorii robota (niezbędna jest praca człowieka bezpośrednio przy robocie), możliwe jest załączenie napędów manipulatora, ale tylko w momencie kiedy operator trzyma wciśniętą płytkę zezwolenia na panelu programowania robota. Jej zwolnienie lub wciśnięcie do końca powoduje natychmiastowe wyłączenie napędów, a osie manipulatora zatrzymywane są w danej pozycji przez hamulce.
Same korzyści
Zrealizowana przez Pro-Zap aplikacja jest przykładem stanowiska bardzo nowoczesnego, niezawodnego, zapewniającego wysoką jakość, powtarzalność produkowanych detali oraz dużą elastyczność – niewielkim kosztem można dostosować je do produkcji innych podzespołów. Jednocześnie, stanowisko jest proste w obsłudze i atrakcyjne cenowo poprzez bardzo precyzyjne dostosowanie funkcjonalności do specyficznych wymagań procesu spawania. To właśnie względy funkcjonalne i ekonomiczne dają użytkownikowi podstawy do planowanego, szybkiego zwrotu inwestycji.