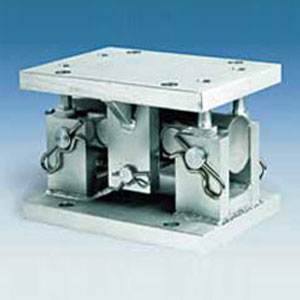
Pomiar masy jest chyba najczęściej stosowanym pomiarem w gospodarce. Ważyć można wszystko – od surowców naturalnych i materiałów budowlanych, poprzez zboża i prefabrykaty spożywcze, na cieczach kończąc. To właśnie z racji różnorodności materiałów, których masa jest ważnym parametrem, istnieje szereg specjalistycznych, daleko różniących się od siebie typów wag. Najczęściej stosowane w przemyśle – ze względu na skalę zastosowań określonych układów transportu i magazynowania – są wagi zbiornikowe.
TYTUŁEM WSTĘPU
Wagi zbiornikowe opierają swoje działanie na czujnikach tensometrycznych i są to zbiorniki z możliwością posadowienia na od 3 do kilkunastu tzw. „węzłach czujnikowych” – czujnik tensometryczny z zabudową. Sygnały z przetworników sumuje się w skrzynce połączeniowej, a następnie sygnał przekazywany jest do terminala wagowego. Są to urządzenia do pracy w przemyśle, a także w zakładach produkcyjnych wytwarzających zarówno materiały sypkie jak i płynne. Stosowane są do określenia masy w zbiorniku/silosie. Możliwe jest również sterowanie np. zaworami, klapami w celu wykonywania dozowań czy automatyzacji i wizualizacji procesów przemysłowych. System ważenia zbiorników może zostać wdrożony zarówno do istniejących obiektów jak i do obiektów nowo projektowanych.
PROBLEMY I ICH ROZWIĄZANIA
Pewien problem w przypadku wag zbiornikowych stanowi instalacja napełniania lub opróżniania (w szczególności sztywne połączenia rurowe z otoczeniem). Ponieważ tego typu połączenia mogą mieć wpływ na dokładność ważenia, w tego typu przypadkach należy zastosować różnego rodzaju elastyczne kompensatory minimalizujące wpływ połączeń elastycznych na dokładność ważenia.
Realizacja wag zbiornikowych na niskie nominały nie stanowi większego problemu szczególnie w sytuacjach, w których możliwe jest obciążenie zbiornika ciężarkami wzorcowymi lub wlanie/wsypanie znanej, odważonej ilości materiału na wadze kontrolnej. Problem pojawia się przy ważeniu bardzo dużych silosów/tanków o bardzo dużej nośności, nawet do kilku tysięcy ton. W takich przypadkach niemożliwe jest obciążenie silosu ciężarkami wzorcowymi w celu ich skalibrowania. Wlanie/wsypanie odważonej porcji materiału na wadze kontrolnej jest czasochłonne i obarczone błędem – zastanówcie się Państwo jaki błąd popełnimy dla kilkudziesięciu odważeń na wadze kontrolnej (np. wadze samochodowej legalizowanej o nośności 60 t z działką pomiarowa e = 20 kg).
Dla przykładu weźmy pod uwagę wagę silosu o nośności 2000 t. Działka pomiarowa (dla 1000 działek): d = 2 t.
Aby skalibrować taką wagę kolejno:
- odważmy 2000 t materiału na wadze samochodowej o parametrach: Q = 60 t, e = 20 kg;
- jeśli wagę chcemy kalibrować przy pełnym obciążeniu musimy odważyć 80 samochodów z materiałem np. po 25 t (jedno ważenie – samochód z towarem i drugie ważenie – samochód pusty);
- dopuszczalny błąd ważenia wagi samochodowej dla obciążeń od 10 t do 40 t wynosi ±20 kg, powyżej 40 t błąd dopuszczalny ±30 kg;
- ważenie samochodu z towarem może być obarczone błędem ±30 kg, ważenie samochodu pustego ±20 kg;
Zatem błąd dla jednej porcji materiału może wynieść 50 kg, a łączny błąd dla 85 porcji materiału może wynieść 80·50 kg = 4 t – czyli 2 działki pomiarowe d. Jeśli chcemy uzyskać dokładność 0,1% maksymalnej nośności wagi nie powinniśmy popełnić błędu dla maksymalnej nośności większego niż 2000 t·0,1% = 2 t.
Istnieje jednak sposób wykonania wagi silosu o bardzo dużej nośności z wykorzystaniem tzw. „kalibracji teoretycznej” na podstawie znajomości charakterystyki czujników, bez wykorzystania ciężarków wzorcowych i odważonej porcji materiału.
W dalszej części artykułu skupimy się na tym właśnie sposobie wykonania wagi silosu o bardzo dużych obciążeniach, doborem „węzłów czujnikowych”, skrzynek połączeniowych i terminali wagowych, tak aby uzyskać dokładność ważenia na poziomie 0,1%.
DOBÓR „WĘZŁÓW CZUJNIKOWYCH”
Na „węzłach czujnikowych” wspiera się cała konstrukcja zbiornika. „Węzły czujnikowe” zabezpieczają zbiornik zarówno przed siłami poprzecznymi, jak i przed podrywaniem, zapewniając jednocześnie dokładny pomiar masy materiału znajdującego się w zbiorniku. Czujniki tensometryczne i zabudowy mogą być w wykonaniu ze stali cynkowanej lub nierdzewnej. Zasada działania czujników jest stosunkowo prosta. Czujnik przekształca siłę nacisku na sygnał analogowy wyrażony w mV/V. Najczęściej spotykane są czujniki o czułości 2 lub 3 mV/V, np. dla czułości 2 mV/V, przy nominalnym obciążeniu (maksymalne obciążenie czujnika), maksymalny sygnał wyjściowy wynosi 2 mV/V na każdy Volt zasilania, czyli dla zasilania czujnika z terminala wagowego równego 10 V maksymalny sygnał z przetwornika wyniesie 20 mV.
Przy obecnym rozwoju elektroniki przetworników analogowo-cyfrowych używanych w terminalach wagowych, można stwierdzić, iż dokładność wagi zależy w głównej mierze od czujników tensometrycznych. O dokładności czujników tensometrycznych świadczy ich klasa.
Dla czujników tensometrycznych o dużych nominałach dokładność może być nie gorsza jak ±0,1% lub mogą to być czujniki klasy C1 (1000 działek). Przy doborze czujników bardzo istotną kwestią jest ich nominał. W tym celu musimy znać na ilu czujnikach posadowiony zostanie silos i jakie będzie obciążenie maksymalne silosu (netto + tara).
Dla przykładu weźmy silos o obciążeniu maksymalnym 2000 t, przy 12 czujnikach tensometrycznych. Czujniki musimy dobrać na taką nośność aby maksymalne obciążenie silosu (2000 t) stanowiło od 1 do 1 sumy nośności czujników (Scz), czyli Scz = od 4000 t do 8000 t.
Przykłady czujników o dużej nośności:
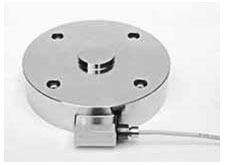
a) czujnik ściskany CBLS (200t-750t) dokładność ≤0,1%
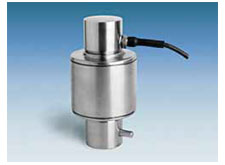
b) czujnik kolumnowy M-740 (15t-600t) dokładność: od 15t do 60t klasa C4 od 100t do 600t klasa C1
W takim przypadku należy zastosować np. 12 szt. czujników o obciążeniu 400 t każdy, co daje 12·400 t = 4800 t. Należy zwrócić również w tym miejscu uwagę, iż dodatkowo każdy czujnik ma dopuszczalną przeciążalność 150% nośności nominalnej z tym, że dokładność katalogowa jest gwarantowana do 100% obciążenia. Przy doborze zabudowy czujników należy wziąć pod uwagę, iż silosy o bardzo dużych pojemnościach mają duże gabaryty i w związku z tym musimy uwzględnić wpływ rozszerzalności cieplej zmieniającej wymiary poziome punków podparcia „węzłów pomiarowych”. Wpływ rozszerzalności cieplej będzie do pominięcia w przypadku gdy „węzły pomiarowe” instalowane będą pomiędzy dwoma pierścieniami stalowymi lub na płycie żelbetowej (podobna rozszerzalność termiczna dla stali i płyty żelbetowej).
Problem pojawia się gdy „węzły czujnikowe” podparte są na niezależnych słupach np. wkopanych w grunt. W tym przypadku zabudowa musi umożliwić kilkumilimetrowe przemieszczenie w poziomie (w kierunku promienia silosu) tak aby nie zmienić parametrów metrologicznych czujników.
Proponowane przez nas „węzły czujnikowe” zabezpieczają dodatkowo silos przed siłami poprzecznymi i przed podrywaniem, zapewniając jednocześnie dokładny pomiar masy materiału znajdującego się w zbiorniku.
Poniżej przedstawiano dwa rodzaje zabudów, które spełniają to wymaganie eliminując wpływ rozszerzalności cieplnej na dokładność ważenia.
Przykłady zabudowy:
b) zabudowa do czujnika kolumnowego z odciągiem – zabudowę należy instalować tak aby odciąg zabudowy był ustawiony prostopadle do promienia silosu.
DOBÓR SKRZYNEK POŁĄCZENIOWYCH
Aby uzyskać dużą dokładność wagi należy spełnić pewne warunki, a jednym z nich jest wyrównanie czułości wszystkich użytych czujników do pomiaru masy. Większość producentów czujników tensometrycznych dostarcza czujniki o czułości 2 lub 3 mV/V z dokładnością ±0,1%. Weźmy dla przykładu dwa czujniki o nośności 400 t i czułości 2 mV/V (jeden +0,1% i drugi -0,1%).
- czujnik 1: czułość = 2,002 mV/V,
- czujnik 2: czułość = 1,998 mV/V.
Załóżmy, że zasilanie czujników z terminala wagowego wynosi 10 V. Mamy zatem dla obciążenia równego 1 nośności czujnika (100 t) sygnały:
- czujnik 1:10 V·2,002 mV/V·1 = 5,005 mV,
- czujnik 2:10 V·1,998 mV/V·1 = 4,995 mV.
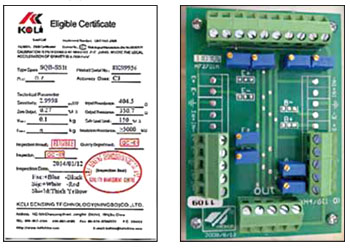
Świadectwo kalibracji czujników i płytka skrzynki połączeniowej z potencjometrami do regulacji czułości
Załóżmy znowu, że średnia wartość czułości dla wszystkich czujników wynosi 2 mV/V. Zakres sygnału użytecznego dla 2000 t wyniesie (10 V·2 mV/V)·(2000 t)/(12·400 t) = 8,33 mV.
Czyli na jedną działkę pomiarową d = 2 t przypada sygnał o wartości 8,33 mV/1000 = 0,008 mV. Jeśli zatem nacisk na czujnik 1 i czujnik 2 jest taki sam (100 t) to różnica sygnału generowanego przez te dwa czujniki wynosi 5,005 mV-4,995 mV = 0,01 mV, czyli więcej niż dla jednej działki pomiarowej. Z tego wynika, iż aby uzyskać dokładność = 0,1% należy wyrównać czułości wszystkich czujników użytych w wadze. W tym celu należy zastosować skrzynki połączeniowe z możliwością regulacji czułości czujników (z potencjometrami wpiętymi w szereg z napięciem zasilania czujników).
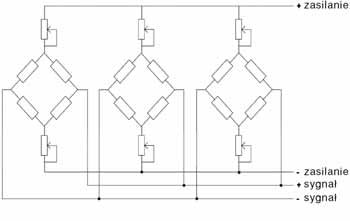
Przykład wpięcia potencjometrów w szereg z zasilaniem czujników tensometrycznych
Dodatkowo musimy posiadać świadectwa kalibracji każdego czujnika użytego w wadze. Na podstawie świadectwa kalibracji czujnika możemy odczytać:
- Czx – czułość czujnika x,
- Rwejx – rezystancja wejściowa czujnika x.
Spośród użytych czujników do wykonania wagi wybieramy czujnik o najmniejszej czułości:
Czn – czułość najmniejsza czujnika dla zestawu czujników użytych w wadze.
Wszystkie wartości czułości pozostałych czujników obniżamy do wartości Czn poprzez włączenie w szereg napięcia zasilania poszczególnych czujników rezystancji obliczonej według poniższego wzoru:
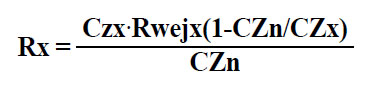
- Rx – rezystancja do ustawienia na potencjometrze dla czujnika x,
- Czx – czułość czujnika x,
- Rwejx – rezystancja wejściowa czujnika x,
- Czn – czułość najmniejsza czujnika dla zestawu czujników użytych w wadze.
DOBÓR TERMINALI WAGOWYCH
Ponieważ dla dużych obciążeń niemożliwe jest nałożenie wzorców na zbiornik/silos, a zapełnienie zbiorników odważoną, ogromną porcją materiału jest albo niemożliwe albo nie zapewnia dokładności odważonej łącznej masy 0,1%, musimy zastosować terminal wagowy z możliwością przeprowadzenia „kalibracji teoretycznej”.
Aby zrealizować „kalibrację teoretyczną” należy wpisać w parametry terminala następujące parametry:
- suma nominalnych obciążeń użytych czujników w wadze (ilość czujników · nominalne obciążenie każdego czujnika);
- czułość czujników (podajemy wartość czułości Czn – czułość najmniejsza czujnika dla zestawu czujników użytych w wadze) – oczywiście pod warunkiem wcześniejszego wykonania wyrównania czułości wszystkich czujników w skrzynce połączeniowej;
- wartość szacunkowa pustego zbiornika/silosu;
- na koniec należy wykonać „rekalibrację zera wagi” uwzględniającą rzeczywistą masę pustego zbiornika.
Przykłady terminali wagowych z funkcją „kalibracji teoretycznej”:
Terminale wagowe oprócz wskazywania masy w silosie umożliwiają również komunikację z systemem nadrzędnym sterującym procesem produkcyjnym. Wyposażone w wyjścia RS232, RS485, MOD-BUS, Profibus, Ethernet czy wyjście analogowe 4÷20 mA umożliwiają podłączenie do PC, na którym można wykonywać wizualizacje i archiwizację danych; tudzież do sterownika w celu realizacji zarządzania np. procesami naważania.
SPECJALIŚCI OD OGROMNYCH WAG ZBIORNIKOWYCH
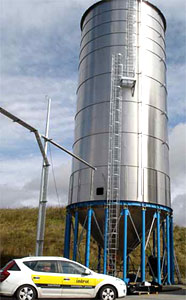
Przykład zrealizowanej wagi zbiornikowej – nośność 600t
Jeśli do wykonania wagi bardzo dużego silosu o nośności nawet kilku tysięcy ton, prawidłowo dobierzemy „węzły czujnikowe”, skrzynki połączeniowe i terminale wagowe, to możemy wykonać wagę o wysokiej dokładności, około 0,1%, bez używania ciężarków wzorcowych oraz mozolnie odważanej porcji materiału. Należy przy tym pamiętać, że tylko kompletna wiedza dotycząca aplikacji oraz wymagania dla układu wagowego określone na etapie ekspertyzy technicznej, zapewnią dobór wagi spełniającej wymagania użytkownika. Ze względu na zwiększającą się ilość zapytań dotyczących pomiaru masy w dużych zbiornikach, mam nadzieję, że tych kilka podstawowych informacji przyda się osobom zainteresowanym w przypadku rozbudowy lub modernizacji układów wagowych w ich zakładach. Na zakończenie warto podkreślić, że Dział przemysłowych pomiarów masy INTROL posiada w swojej ofercie kompletne zestawy wagowe (różnych producentów) do pomiaru masy w silosach o dużych nominałach, wykonuje ekspertyzy oraz kompletne dokumentacje.
Jesienią 2010 roku INTROL uruchomił jak dotąd jedną z najcięższych wag zbiornikowych (silos) w Polsce o nośności 600 t, z działką odczytowa d = 0,5 t. W tym układzie wagowym wykorzystano 20 czujników klasy C3 o nośności 50 t każdy. Wyniki pomiarów prezentowane zostały na terminalu wagowym wraz z przesyłem informacji do sterowni. Po montażu całości, przeprowadzono próby materiałowe, potwierdzając zakładaną dokładność pomiaru <0,1% dla całego zakresu pomiarowego.
Doświadczenie zdobyte podczas tej oraz innych realizacji pozwala naszym specjalistom na realizacje jeszcze większych wag zbiornikowych, nawet do kilku tysięcy ton.
autor:
Janusz Cop
jcop@introl.pl