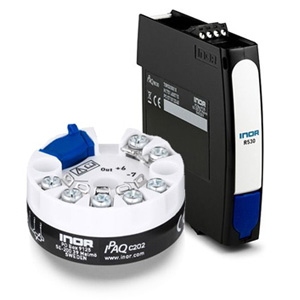
Pomiar temperatury w przemysłowych procesach produkcyjnych jest jednym z najważniejszych parametrów dla osiągnięcia maksymalnej jakości wyrobów i ciągłości produkcyjnej. Dlatego też w zakładach produkcyjnych praktycznie każdy etap produkcji opiera się na pomiarze temperatury, od którego uzależnionych jest kilka innych działań w dalszym etapie produkcyjnym. Bardzo istotnym jest więc, aby urządzenia pomiarowe, w tym przypadku przemysłowe czujniki temperatury, były odpowiednio dobrane i spełniały restrykcyjne wymogi związane z prawidłowym pomiarem. Samo założenie mówiące o tym, że urządzenie powinno poprawnie mierzyć jest połową sukcesu. Kolejnym etapem jest obsługa i możliwość nadzorowania jego pracy. W tym przypadku z pomocą przychodzą przetworniki temperatury, które umożliwiają użytkownikowi komunikację z urządzeniem.
Skupmy się zatem na odpowiednim doborze czujników temperatury oraz przedstawmy możliwości nowoczesnych przetworników temperatury.
DOBÓR CZUJNIKÓW TEMPERATURY
Każdy proces produkcyjny składa się z wielu różnych etapów. Nigdy nie jest to jeden ciągły proces lecz kilka mniejszych, z połączenia których powstaje produkt finalny. Proces produkcyjny to wszystko to, co prowadzi do powstania gotowego produktu. Tak więc w skład procesu, w wielkim skrócie, wchodzą transport surowca/półproduktu, właściwy proces produkcji, a następnie przechowywanie wyrobu gotowego. Na każdym z tych etapów ważnym jest, aby została zachowana odpowiednia temperatura. Wbrew przekonaniom o pomiarze temperatury, który uznawany jest jeden z najprostszych, dobór czujnika temperatury wcale nie jest taki oczywisty. Składa się na to wiele czynników, takich jak przede wszystkim temperatura jaką planuje się mierzyć, medium, jego gęstość, stan skupienia, struktura czy ciśnienie. To tylko kilka wymienionych parametrów, które mają ogromny wpływ na pomiar, a tym samym na dobór odpowiedniego czujnika.
Planując dobór czujnika należy zwrócić uwagę głównie na medium – czy jest to gaz czy medium ciekłe. Ma to kolosalne znaczenie, ponieważ praktycznie każdy czujnik posiada osłonę, która oddziela właściwy element pomiarowy od mierzonego medium/elementu. W przypadku gazów termodynamika jest znacznie mniejsza niż w przypadku cieczy. Tak więc istotnym jest, aby mierząc gazy osłona była o maksymalnie niskiej średnicy i małej grubości ścianki, aby wymiana temperatury pomiędzy osłoną a medium była jak najszybsza i efektywna. Gęstość gazów jest zazwyczaj dużo niższa od cieczy, dlatego przepływ nie będzie znacząco wpływał na wytrzymałość osłony, więc można stosować mniejsze średnice dla poprawy termodynamiki. Kolejnym krokiem w doborze jest ciśnienie na jakie narażony będzie czujnik temperatury. W większości przypadków, kiedy czujnik jest projektowany dla potrzeb nowych linii produkcyjnych czy też nowo powstałych zakładów, czujniki z reguły są znacząco przewymiarowane jeżeli chodzi o wytrzymałość na ciśnienie. Standardowe czujniki z gwintem przyłączeniowym o długości osłony maksymalnie 160 mm, potrafią wytrzymać ciśnienie rzędu 6 MPa. Czujniki z osłonami ciśnieniowymi stosuje się raczej do ciśnień powyżej tych wartości. Niejednokrotnie niestety spotyka się, że projektowane są czujniki z osłonami ciśnieniowymi dla ciśnienia rzędu 2-3 MPa lub niższych, co nie jest potrzebne i przekłada się znacząco na czas reakcji czujnika. Osłona ciśnieniowa ze względu na swoją konstrukcję ma bowiem bardzo wysoką bezwładność, co z kolei przekłada się na niewłaściwy pomiar temperatury i dalej idące za tym konsekwencje w produkcji.
Kolejnym problemem jaki można napotkać to skład chemicznych mierzonego medium. Jest to bardzo ważny czynnik, który determinuje kształt i materiał do produkcji czujnika temperatury. Oczywiście większość stali, z których wykonuje się osłony czujników sprosta wymaganiom odpornościowym na działanie związków chemicznych. Są to z reguły stale jakościowe, kwasoodporne, które akceptowane są także w przypadku kontaktu z żywnością. Jednakże czasami proces produkcji opiera się na wykorzystaniu związków chemicznych, które są bardzo aktywne i wchodzą w reakcję ze stalą. Wówczas należy pamiętać, aby uwzględnić w doborze czujnika odpowiednią powłokę, która zabezpieczy czujnik przed ewentualnymi uszkodzeniami. Takimi powłokami mogą być tworzywa sztuczne, jak polwinit czy też teflon, który jest bardzo odpornym materiałem. Takie rozwiązanie ma jednak swoje minusy – nie jest odporne na wysoką temperaturę i duże tarcie, dlatego też dobór może być niemożliwy. W takich wypadkach należy stosować materiały nieszablonowe, mało spotykane, a przez to kosztowne. Analizując powyższe uwagi związane z doborem czujnika, wbrew pozorom potwierdza się, iż nie w każdych warunkach jest to łatwy pomiar. Jest wiele aspektów, na które trzeba zwrócić uwagę niejednokrotnie posiłkując się wsparciem technicznym. Należy przy tym zawsze pamiętać aby w specyfikacji podać takie parametry jak: temperatura pracy, medium, długość zanurzenia, średnica, rodzaj przyłącza, ewentualna długość przewodu.
RODZAJE ELEMENTÓW POMIAROWYCH
Wyróżniamy 2 podstawowe typy czujników temperatury: pomiar rezystancji oraz pomiar napięcia. Głównymi elementami pomiarowymi w tych przypadkach są rezystory pomiarowe oraz termoelementy (termopary) w przypadku metody napięciowej. Każdych z nich charakteryzuje się innymi właściwościami temperaturowymi oraz dokładnościami w uzyskanych odczytach. Termoelementy były już kiedyś bardzo precyzyjnie opisane na łamach „Pod Kontrolą”, dlatego też teraz uwagę skupimy na rezystorach pomiarowych.
Rezystory pomiarowe najbardziej spotykane w czujnikach temperatury to typ Pt100, rezystor Pt1000, Pt500, czy też, już rzadziej spotykane, rezystory Ni100, Ni1000 czy Ni500. Zdekodowanie powyższych oznaczeń jest bardzo proste. Oznaczenie literowe oznacza użycie materiałów, mianowicie „Pt” oznacza rezystory z wykorzystaniem platyny, natomiast oznaczenie „Ni” oznacza wykorzystanie niklu. Drugi człon nazwy tj. liczbowe oznaczenie np. 100 oznacza iż, rezystor w 0°C generuje rezystancje na poziomie 100 Ω i analogicznie oznaczenie 1000 to 1000 Ω itd. Najbardziej popularne są rezystory o oznaczeniach „Pt”, czyli z wykorzystaniem platyny i takie też stosuje się powszechnie do produkcji czujników temperatury. Oznaczenie liczbowe jest natomiast bardzo ważne, ponieważ informuje to służby z jaką wielkością rezystancji mają do czynienia w przypadku odczytów, czy też ewentualnych testów poprawności działania na zwykłych multimetrach. Oprócz tego, podłączenie takiego czujnika z odbiornikiem, którym może być wyświetlacz cyfrowy, regulator czy też rejestrator, wiąże się z użyciem przewodu, który również ma swoją rezystancję. Co w takim wypadku ma ze sobą wspólnego rodzaj rezystora, a przewód połączeniowy? Otóż rezystancja w przypadku rezystorów o niskiej liczbie w nazwie (np. Pt100) zmienia się wraz ze zmianą temperatury w przedziale niskich wartości, tak więc w momencie zmiany temperatury o 1°C, odczyt rezystancji zmieni się tylko o dziesiąte części. Dodając do tego rezystancję, która powstanie w przewodzie połączeniowym o znaczącej długości, okazuje się, iż odczyt na urządzeniu odbiorczym będzie obarczony dużo większym błędem niż zakłada klasa samego czujnika. Dlatego też, jeżeli przewidziany jest przewód połączeniowy, który jest bardzo długi, stosuje się raczej rezystory o dużo większej rezystancji, aby w momencie dodania rezystancji przewodu nie powstał duży błąd.
Rezystory pomiarowe wykorzystywane są raczej do niższych temperatur niż termoelementy oraz tam, gdzie wymagana jest maksymalna dokładność. Można uzyskać na tego typu pomiarze dokładność rzędu dziesiętnych °C, co w przypadku termoelementów jest bardzo ciężkie do osiągnięcia, a wręcz niemożliwe.
Minusem rezystorów pomiarowych jest niestety niski górny próg temperaturowy wynoszący ok. +850°C (z praktyki raczej stosuje się w granicach 550 … 600°C plus ograniczenia w budowie czujnika). Zaletą rezystorów jest natomiast dolna granica, która zaczyna się na poziomie -200°C, co nie wymaga żadnego specjalnego wykonania. Zarówno rezystory, jak i termoelementy mają swoich „pomocników” w przesyle sygnału na duże odległości, czy też w komunikacji z nimi. Mowa oczywiście o przetwornikach temperatury.
PRZETWORNIKI TEMPERATURY
Przetworniki temperatury są nieodzownym elementem praktycznie każdego czujnika temperatury. Umożliwiają wyprowadzenie standardowego sygnału automatyki jakim jest sygnał prądowy 4…20 mA do sterowania przy pomocy regulatora czy też sterownika PLC. Jednak oprócz sygnału, przetworniki spełniają również inną funkcję. Pozwalają one bowiem skomunikować się z czujnikiem za pomocą różnego rodzaju protokołów komunikacyjnych, co usprawnia ich
działanie.
KOMUNIKACJA ZA POMOCĄ PROTOKOŁU HART
Jednym ze standardowych protokołów, które można spotkać w przetwornikach jest protokół HART. Jest to cyfrowy sygnał nałożony na sygnał analogowy generowany przez przetwornik. Dzięki takiemu rozwiązaniu można zarówno sterować, jak i odczytywać parametry czujnika, bez konieczności stosowania dodatkowych przewodów połączeniowych. Sygnał ten jest wysoce odporny na zakłócenia. Aby zastosować protokół HART, należy za pomocą odpowiedniego modułu wpiąć się w pętlę prądową sygnału analogowego i w ten sposób nawiązać połączenie z przetwornikiem. Protokół ten pozwala użytkownikowi na odczyty wskazań z czujnika temperatury i wprowadzanie wielu dodatkowych parametrów, jak nr inwentarzowy, nazwę obiektu. Hart umożliwia także wprowadzenie hasła dostępu czy zmianę ustawień z pozycji sterowni. Takie udogodnienie sprawia, że czujnik temperatury staje się urządzeniem, nad którym mamy pełną, zdalną kontrolę.
KONTROLA ZA POMOCĄ NFC
Innym sposobem komunikacji jest NFC znane z technologii nowoczesnych telefonów komórkowych. Rozwiązanie to jest dostępne w najnowszych przetwornikach INOR’a. Jest to kamień milowy w komunikacji z tego rodzaju urządzeniami. Praktycznie wystarczy użytkownikowi aby miał zamontowany przetwornik z tego typu komunikacją w swoim czujniku temperatury i posiadał smartfon z możliwością komunikacji po NFC.
Oprogramowanie jest ogólnodostępne w popularnych sklepach internetowych w systemie Android jak i iOS. Komunikacja w ten sposób sprawia, że zarządzanie pomiarem temperatury nigdy nie było tak proste i przyjazne dla młodych inżynierów, którzy przecież obsługę NFC znają od podszewki. Za pomocą oprogramowania odczytane zostają nastawy przetwornika, można również zmienić zakresy sygnału analogowego, jak i wprowadzić wewnętrzne oznaczenia dla danego punktu pomiarowego. Całość współpracuje ze standardowymi sygnałami analogowymi i protokołami komunikacyjnymi, w tym HART.

Oprogramowanie INOR na smartfon
KOMUNIKACJA BLUETOOTH
Bluetooth jest już dobrze znanym sposobem przekazu informacji na niewielkie odległości. Firma INOR stworzyła nowoczesny komunikator, który wykorzystuje technologię Bluetooth i w tym przypadku jest on niezbędny do skomunikowania się przetwornika ze smartfonem (nie ma wbudowanego modułu bluetooth w przetwornikach). Komunikuje się on praktycznie z każdym przetwornikiem tej marki z serii IPAQ. Jak wspominałem, do komunikacji z przetwornikiem potrzebny jest specjalny komunikator, który podłączany jest do przetwornika poprzez kabel USB.
Może być on zarówno integralną częścią każdego urządzenia, jak i systemem przenośnym, wykorzystywanym tylko w razie potrzeby. Komunikacja bezprzewodowa usprawnia przede wszystkim działania wszystkim służbom pracującym z tymi urządzeniami. Pozwala ona na wprowadzanie zmian bez konieczności stosowania dodatkowych przewodów, czy też uciążliwej mobilnej pracy na komputerze przy czujniku, w trakcie produkcji.

Zestaw do komunikacji bluetooth
KROK W STRONĘ PRZYSZŁOŚCI
Pomiar temperatury zawsze był i myślę, że nadal będzie bardzo ważnym aspektem w produkcji czy innych dziedzinach przemysłu. Należy zatem odpowiednio zadbać o poprawny jego pomiar. Warto także stosować nowoczesne technologie komunikacji, które usprawniają zarządzanie tym pomiarem. Nie należy się ich obawiać, a wręcz przeciwnie – stosować je jak najszerzej, nawet w tak klasycznych pomiarach jak temperatura. W dobie rozwijającego się przemysłu 4.0 także klasyczne pomiary będą bowiem odgrywać znaczącą rolę, a nowoczesna komunikacja pozwoli na wejście w ten czas z dużą dozą uzyskanego już doświadczenia