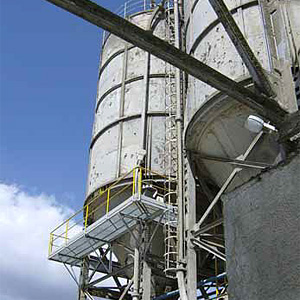
W oparciu o wyniki pracy instalacji dozującej pyły z by’passu1 do młyna cementu w Cementowni REJOWIEC.
W wielu procesach przemysłowych powstają materiały sypkie i pylaste, które są produktem końcowym (cement, wapno, nawozy sztuczne itp. materiały) lub materiały odpadowe (popioły lotne, pyły z odpylania i odsiarczania spalin z kotłów i pieców przemysłowych itp.). Produkcja materiałów sypkich i pylastych lub powstawanie odpadów o takiej konsystencji w procesach przemysłowych zawsze wiąże się z koniecznością transportowania ich wewnątrz zakładów pomiędzy obiektami instalacji technologicznych.
PROBLEMY ZWIĄZANE Z WEWNĄTRZZAKŁADOWYM TRANSPORTEM MATERIAŁÓW SYPKICH I PYLASTYCH (o bardzo wysokim stopniu rozdrobnienia)
O ile do wewnątrzzakładowego transportu materiałów sypkich można wykorzystać większość typowych przenośników (przenośniki taśmowe, ślimakowe, zgrzebłowe, kubełkowe itp.), o tyle w transporcie materiałów pylastych urządzenia te w większości zawodzą. Problem z transportem materiałów pylastych jest najbardziej uciążliwy gdy wymagany jest transport na znaczne odległości (rzędu kilkudziesięciu do kilkuset metrów) i przy skomplikowanej konfiguracji trasy transportowej. Ponadto, transport takich materiałów powinien być w pełni hermetyczny ze względu na wtórną emisję pyłów do środowiska (szczególnie w przypadkach, gdy pyły mają własności toksyczne).
Właściwości transportu pneumatycznego sprawiają, że to właśnie ta metoda w największym stopniu spełnia wymagania związane z przemieszczaniem materiałów sypkich, a zwłaszcza materiałów pylastych.
ZALETY I WADY TRANSPORTU PNEUMATYCZNEGO W PRZEMIESZCZANIU MATERIAŁÓW SYPKICH I PYLASTYCH
Transport pneumatyczny polega na przekazaniu energii sprężonego powietrza do strumienia materiału sypkiego w rurociągu transportowym. Spełnienie tego warunku wymaga podania materiału sypkiego z przestrzeni o ciśnieniu otoczenia (zbiornik) do przestrzeni o ciśnieniu sprężonego powietrza transportującego (rurociąg transportowy).
W transporcie pneumatycznym wykorzystywane są różne urządzenia, których zadaniem jest podanie materiału sypkiego z przestrzeni o niskim ciśnieniu do przestrzeni o ciśnieniu wysokim. Poniżej przedstawiamy zalety i wady poszczególnych rozwiązań w tym zakresie:
- Podawacz celkowy z otwartym rotorem i przedmuchem celek
Rozwiązanie najprostsze i tanie. Teoretycznie stwarza możliwość rozbudowy o kontrolę strumienia materiału transportowanego. Jest to jednak rozwiązanie wrażliwe na „zatarcie”, szczególnie w transporcie materiałów pylastych. Ponadto, w przypadku materiałów o własnościach ściernych, podawacz szybko rozszczelnia się, co powoduje rosnące przecieki sprężonego powietrza do zbiornika nad podawaczem i pogarsza warunki transportu, aż do „zatkania” rurociągu włącznie. Rozwiązanie w zasadzie nie nadaje się do pracy ciągłej. - Podawacz komorowy
Jedno z najstarszych i sprawdzonych rozwiązań. Dobrze odcina przestrzeń ciśnienia niskiego od przestrzeni ciśnienia wysokiego (minimalne przecieki wsteczne), ale ze względu na cykliczną pracę, wyklucza aktywną kontrolę strumienia transportowanego materiału. Podawacz komorowy wymaga najwyższych ciśnień powietrza transportującego (4 do 7 bar), co wydatnie podnosi energochłonność jednostkową transportu, a ze względu na cykliczność pracy zwiększa się ryzyko „zapchania” rurociągu transportowego. - Pompa Fullera
W tym rozwiązaniu przestrzenie o różnym ciśnieniu oddzielone są za pomocą „korka” utworzonego z materiału sypkiego przez szybkoobrotowy ślimak pompy. Pompa Fullera zapewnia ciągłą pracę transportu, ale wyklucza możliwość aktywnej kontroli strumienia materiału transportowanego. Ponadto, części wirujące ulegają szybkiemu zużyciu, a sam proces tworzenia „korka” jest bardzo energochłonny. Moc silnika napędowego pompy porównywalna jest z mocą silnika sprężarki zasilającej transport. Pod względem energetycznym i serwisowym pompa Fullera jest rozwiązaniem najdroższym. - Podawacz celkowy z podwójnym otwartym rotorem poziomym i pionowym przedmuchem celki
Stosunkowo nowe rozwiązanie. Wyposażone w poprzeczną wagę tensometryczną stwarza możliwość dokładnej (0,5% do 1%) kontroli strumienia materiału transportowanego. Dobrze sprawdza się w zastosowaniu do materiałów o stosunkowo małym stopniu rozdrobnienia (powierzchnia właściwa wg Blaine’a poniżej 3800 cm²/g). Przy materiałach pylastych (powierzchnia właściwa wg Blaine’a powyżej 4000 cm²/g) zachodzi bardzo duże ryzyko zatarcia rotora i awaryjnego zniszczenia podawacza.
POWODY POWSTANIA INSTALACJI DOZUJĄCEJ PYŁY Z BY’PASSU DO MŁYNA CEMENTU W CEMENTOWNI REJOWIEC
Zakład Cementownia REJOWIEC wchodzi w skład Grupy OŻARÓW S.A., w której wiodącym zakładem jest Cementownia OŻARÓW. W trakcie modernizacji pieca obrotowego w Cementowni OŻARÓW, w celu podniesienia jakości klinkieru cementowego, zbudowany został tzw. by’pass chemiczny mający za zadanie usunięcie nadmiaru związków alkalicznych z pieca. Związki te sublimują na ziarnach mąki surowcowej w instalacji by’passu i w postaci pyłów wyprowadzane są na zewnątrz instalacji. Jako odpad pyły te nie mogą być składowane i dlatego opracowano recepturę produkcji na ich bazie nowego spoiwa pod nazwą Reymix-Stabilizacja. Produkt ten uzyskał aprobatę Instytutu Dróg i Mostów w Warszawie. Po uzyskaniu w/w aprobaty pilnym problemem stała się budowa linii technologicznej zdolnej do zagospodarowania ok. 20.000 ton pyłów rocznie. Ze względów logistycznych produkcję Reymixu-Stabilizacji zlokalizowano w Cementowni REJOWIEC. Z uwagi na konieczność minimalizacji kosztów przedsięwzięcia, zapadła decyzja o maksymalnym wykorzystaniu w budowie nowej instalacji istniejącej infrastruktury i urządzeń znajdujących się w Zakładzie REJOWIEC.

Zabudowany przepływomierz do pyłu
OPIS INSTALACJI DOZUJĄCEJ PYŁY Z BY’PASSU DO MŁYNA CEMENTU W CEMENTOWNI REJOWIEC
Jako magazyn pyłów by’passowych w Zakładzie REJOWIEC wykorzystano 2 istniejące zbiorniki stalowe o pojemności po 300 m³ każdy, do których pyły dostarczane są z Zakładu OŻARÓW cysternami samochodowymi. Do produkcji nowego spoiwa zaadaptowano jeden z młynów cementu o wydajności ok. 25 t/h. Młyn cementu posiada na wlocie trzy wagoprzenośniki surowców, które kontrolują skład procentowy i ilość podawanych surowców. Strumień podawanych do nitki technologicznej tego młyna pyłów z by’passu, zgodnie z opracowaną recepturą, również musiał być kontrolowany i zsynchronizowany z podawanymi na wlot młyna surowcami. Dodatkowymi utrudnieniami były: odległość zbiorników od młyna (ok. 300 m) i bardzo wysoki stopień rozdrobnienia pyłów (powierzchnia właściwa wg Blaine’a powyżej 7000 cm²/g).
Pierwszy czynnik determinował wykorzystanie wyłącznie transportu pneumatycznego do transportu pyłów ze zbiorników do młyna cementu, drugi czynnik wykluczał możliwość zastosowania typowych rozwiązań wykorzystywanych w tym transporcie. W celu spełnienia poczynionych założeń projektowych, zaprojektowany został transport pneumatyczny pyłów o następujących parametrach Długość trasy – 300 m Średnica rurociągu – DN 125 mm Parametry sprężarki powietrza – Q=1000m³/h; p=2,5 bar Ponadto, zaprojektowano i wykonano pompę celkową z zamkniętym rotorem doszczelnianym regulowaną zworą, umożliwiającą, w razie konieczności, doszczelnienie rotora w trakcie normalnej pracy pompy. Pompa napędzana jest za pośrednictwem przetwornika częstotliwości (moc napędu 2,2 kW).

Zbiorniki stalowe
Pod pompą umieszczono aparat wydmuchowy wyposażony w tak zaprojektowane dysze, aby cała dostępna moc sprężonego powietrza mogła być wykorzystana do dokładnego wymieszania powietrza z pyłem i nadaniu powstałemu strumieniowi mieszaniny pyłowo-powietrznej maksymalnego pędu. Parametry pracy głównej dyszy zasilającej aparat wydmuchowy zostały tak dobrane, aby w maksymalnie możliwym stopniu obniżyć ciśnienie w komorze rotora pompy. W efekcie, całkowicie wyeliminowano przedostawanie się pyłów do otoczenia poprzez uszczelnienie wału napędowego pompy. Do kontroli strumienia pyłów (kontrola obrotów rotora pompy celkowej w czasie rzeczywistym, w automatyce z wagoprzenośnikiem klinkieru cementowego na wlocie młyna cementu) wykorzystany został przepływomierz masowy QantiMass firmy M-Monitor.
Cały system automatyki pracy pompy celkowej, sygnalizacji pracy i raportowania wyników produkcji Reymixu-Stabilizacji i zużycia surowców w tym pyłów z by’passu zaprojektowała i wykonała spółka INTROL z Katowic.
SYSTEM STEROWANIA I RAPORTOWANIA
Wykonany system sterowania w swym podstawowym założeniu ma służyć do uzyskania proporcjonalnego dozowania pyłów z by’passu do strumienia składników w ciągu technologicznym, wykorzystywanym do produkcji Reymixu-Stabilizacji. Tak postawione zadanie, z punktu widzenia samego układu regulacyjnego, sprawia wrażenie prostego i nie odbiegającego od typowych aplikacji. Jednak własności dozowanej substancji jak i specyfika zakładu powodują powstanie szeregu trudności, które należało pokonać podczas realizacji zadania.
Pierwszym i najpoważniejszym problemem było określenie sposobu pomiaru strumienia pyłu dostarczanego do procesu. Problem drugi wynikał z dużych odległości pomiędzy źródłem pyłu jakim są silosy magazynowe, a odbiornikiem – młynem cementu. Jakość dozowania w znacznej mierze uzależniona jest od dokładności określenia natężenia przepływu substancji dozowanej. Typowe powszechnie stosowane metody ciągłego dozowania substancji pylastych, bazują na dozowaniu masowym, realizowanym za pomocą wagoprzenośników. Urządzenia te oferują względnie dużą dynamikę odpowiedzi i dokładność pomiaru, co pozwala w prosty sposób uzyskać dobre parametry wyjściowe układu regulacji. Niestety, w opisywanym przypadku, ze względu na przytoczone wyżej własności substancji dozowanej, zastosowanie wagoprzenośnika nie było możliwe.
Drugą powszechnie stosowaną metodą jest dozowanie objętościowe realizowane za pomocą całego szeregu dostępnych rynkowo urządzeń. Dozowanie objętościowe charakteryzuje się bardzo istotnym mankamentem – nie uwzględnia zmian gęstości (koncentracji) dozowanej substancji. Zmiany koncentracji mogą być powodowane wieloma czynnikami, w opisywanym przypadku wynikają ze zmian poziomu wypełnienia silosu magazynowego. Zainstalowane radarowe mierniki poziomu VEGAPULS oraz system pomiaru masy DGTQ DiniArgeo pozwoliły na oszacowanie występujących zmian koncentracji pyłu. Stwierdzono, iż pomimo działania systemu ciągłego napowietrzania (aeracji) silosów, współczynnik zmiany koncentracji pyłu, w skrajnym przypadku, może osiągnąć wartość z przedziału (1:2,5; 1:3,5). W praktyce oznacza to, iż przy stałej prędkości obrotowej wirnika podajnika, ilość podawanej masy pyłu może zmienić się nawet trzykrotnie.
W zrealizowanym układzie zastosowano przepływomierz masowy do pyłów QantiMass Pro firmy Monitor Technologies. Urządzenie generuje sygnał proporcjonalny do masowego natężenia przepływu pyłu w rurociągu transportowym. Sygnał ten został wprowadzony na wejście regulatora zbudowanego w oparciu o sterownik CompactLogix L1 produkcji Rockwell Automation. Cechą charakterystyczną sterowników serii CompactLogix jest przystosowanie do budowy rozległych układów regulacyjnych, w których istotną rolę odgrywają zdalne moduły obiektowe tzw. wyspy (Point), będące integralną częścią przestrzeni wejść i wyjść jednostki centralnej. Komunikacja między modułami zdalnymi a jednostką centralną odbywa się poprzez dedykowaną sieć ETHERNET. W omawianym przykładzie, sieć komunikacji wewnętrznej sterownika zrealizowano przy użyciu światłowodu o łącznej długości rzędu 800 m.

Sterowniki zabudowane w szafce
Do układu regulacyjnego wprowadzono również sygnały z istniejących wagoprzenośników klinkieru, gipsu i dodatków. Czynnikiem wiodącym w procesie technologicznym jest natężenie przepływu masowego strumienia klinkieru podawanego do młyna. Do wizualizacji i raportowania wykorzystano system Factory Talk View Site Edition produkcji Rockwell Automation. System sterowania pozwala obsłudze na kontrolę wszystkich istotnych parametrów procesu produkcyjnego. Wdrożony system receptur ułatwia utrzymanie stałych i powtarzalnych parametrów produktu końcowego.

Wizualizacja systemu dozowania
PODSUMOWANIE
Wykonana linia do produkcji Reymixu-Stabilizacji w Cementowni REJOWIEC pracuje od początku maja 2016. W tym czasie wyprodukowano 34 000 ton produktu i zużyto do jego produkcji 6 100 ton pyłów. Potwierdzone zostały założenia projektowe dotyczące wydajności pompy celkowej w całym zakresie regulacji (3 do 10 t/h) i dokładności dozowania (±3% od wartości zadanej).
Zastosowany w Cementowni REJOWIEC system można adaptować na inne materiały sypkie i pylaste i dla innych (większych lub mniejszych) wydajności w zależności od potencjalnych potrzeb.
1 pyły z by’passu chemicznego – odpad powstający w procesie wypału klinkieru cementowego w piecu obrotowym
autor:
Jan Hałaj
Maciej Wawrzyszko
mwawrzyszko@introl.pl