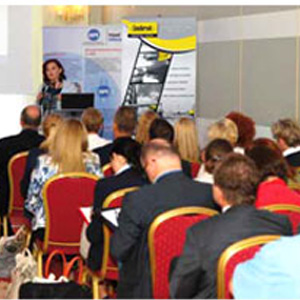
W nowym roku wracamy z cyklem szkoleń dotyczących programowania sterowników kompaktowych SG2 firmy TECO. Najnowsza odsłona szkolenia nawiązuje w pewnym stopniu do poprzedniego artykułu, czyli problemu integracji urządzeń. Postanowiliśmy pokazać rzeczywiste zastosowanie przekaźników programowalnych na przykładzie systemu pomiarowo – alarmowego, zrealizowanego oraz uruchomionego przez nas w jednej z fabryk na terenie Górnośląskiego Okręgu Przemysłowego. Informacje przedstawione w niniejszym szkoleniu stanowią niejako podsumowanie przedstawionych do tej pory zagadnień. W połączeniu z opisem realizacji rzeczywistej aplikacji przemysłowej stanowią bardzo dobre potwierdzenie możliwości funkcjonalnych sterownika SG2.
ZAŁOŻENIA SYSTEMU POMIAROWEGO
W zależności od charakteru wytwarzanego produktu oraz jego przynależności do jednej z wielu grup towarów, wymogi dotyczące linii produkcyjnej mogą się diametralnie różnić.
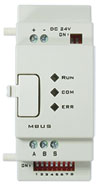
Ilustracja nr 2
Dokładna specyfikacja wymogów zawarta w normach dotyczących jakości wymusza na producentach przestrzegania często surowych warunków produkcji. Wymogi te przybierają szczególną formę w przypadku gdy mamy do czynienia z gałęziami przemysłu, takimi jak przemysł spożywczy lub farmaceutyczny. Jako rzeczywisty przykład możemy podać konieczność doprowadzenia nawiewu czystego, filtrowanego powietrza tuż nad wytwarzany produkt spożywczy. Aby założenia zapisane w normach były spełnione, prędkość powietrza musi zawierać się w ściśle określonych granicach. Zapytanie ofertowe od Klienta dotyczyło systemu pomiaru prędkości przepływu oraz różnicy ciśnień przed i za filtrem powietrza. Przepływ odfiltrowanego powietrza powoduje powstanie nadciśnienia w obszarze znajdującym się ponad produktem spożywczym. Sytuacja taka zapobiega przedostaniu się nieczystości, które mogą znajdować się w obrębie maszyny produkcyjnej.
Przetwornik różnicy ciśnień kontroluje dodatkowo stan zużycia filtru. W zależności od wskazania, jesteśmy w stanie stwierdzić jego poprawną pracę, a także ewentualne zapchanie lub nawet przerwanie. Dodatkowym założeniem aplikacji był moduł alarmowania, uaktywniający się w przypadku wystąpienia jakiegokolwiek potencjalnie niepoprawnego stanu wyżej wymienionych parametrów (przepływu powietrza oraz różnicy ciśnień). Istotnym warunkiem była prosta obsługa oraz intuicyjna parametryzacja systemu przez operatora danej linii produkcyjnej.
INTEGRACJA URZĄDZEŃ
Analiza założeń stawianych przed projektowanym systemem pomiarowo – alarmowym pozwoliła stwierdzić, iż uzasadnione będzie oparcie aplikacji na kompaktowych sterownikach SG2.
Same jednostki centralne musiały jednak zostać doposażone w odpowiednie moduły rozszerzeń, które realizowały funkcje niezbędne do poprawnego działania całego systemu:
- moduł wejść analogowych SG2-4AI rozszerzający ilość kanałów analogowych do sześciu,
- moduł komunikacyjny SG2-MBUS, wyposażony w obsługę protokołu MODBUS RTU i obsługujący transmisję danych pomiędzy urządzeniami.
Integracja jednostki centralnej z modułami rozszerzeń odbywa się automatycznie w momencie ich fizycznego połączenia przy pomocy łączników dodanych do każdego z modułów. W pierwszej kolejności podpinamy moduł analogowy, następnie moduł komunikacyjny. Oprócz sterownika oraz jego rozszerzeń, niezbędnym elementem aplikacji był panel operatorski, służący do łatwego parametryzowania, wyświetlania aktualnych pomiarów oraz powiadamiania o ich ewentualnych, nieprawidłowych wartościach. W zależności od konkretnej maszyny, system obejmował maksymalnie trzy przetworniki różnicy ciśnień oraz dwa przetworniki prędkości powietrza. Różnice w ilości sygnałów pomiarowych wynikały głównie z typu linii produkcyjnej oraz jej rozmiarów. Podłączenie przetworników pomiarowych do sterownika zrealizowane zostało poprzez wpięcie ich w tzw. pętlę prądową 4 … 20 mA. W przypadku tego sygnału pomiarowego, wejścia modułu analogowego mierzą spadek napięcia na precyzyjnym rezystorze pomiarowym, dlatego też konieczne jest odpowiednie podłączenie przewodów.
Zamiast standardowego połączenia dwuprzewodowego, łączony jest dodatkowo trzeci, „informujący” sterownik o pomiarze prądu (dla odróżnienia od pomiaru napięcia, realizowanego dwuprzewodowo).
Komunikacja pomiędzy sterownikiem a dotykowym panelem operatorskim zrealizowana została poprzez dwuprzewodowy interfejs szeregowy RS485.
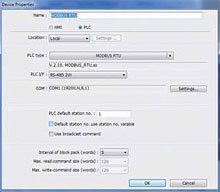
Ilustracja nr 2
Ze względu na zastosowanie tylko dwóch komunikujących się ze sobą urządzeń, połączone one zostały bezpośrednio (nie było konieczności tworzenia rozgałęzionej sieci).
Jak już wcześniej wspomniano, wykorzystany został protokół MODBUS RTU w następującej konfiguracji: sterownik jako urządzenie typu slave oraz panel jako urządzenie nadrzędne typu master. Wybór parametrów komunikacyjnych po stronie sterownika realizowany był poprzez wykorzystanie przełączników dip-switch na module SG2-MBUS. W zależności od binarnego ustawienia jednego z ośmiu przełączników, programista dokonywał wyboru prędkości transmisji danych, kontroli parzystości oraz ilości bitów stopu. W przypadku panelu operatorskiego, obligatoryjne było ustawienie dokładnie tych samych parametrów, jednakże sam proces parametryzacji realizowany był programowo w projekcie wizualizacji (ilustracja nr 2).
PROGRAMOWANIE APLIKACJI
Sterownik Po podłączenia pętli pomiarowej do modułu wejść analogowych sterownika, wartości pomiarowe są od razu dostępne z poziomu środowiska programistycznego. Aby określić czy dany pomiar znajduje się w dopuszczalnym zakresie, wykorzystana zostały komparatory wartości analogowych (ilustracje nr 3, 4).
Pierwsza z ilustracji obrazuje kontrolę wartości pomiarowych dla trzech przetworników różnicy ciśnień. Komparatory G01,G02 oraz G03 ustawione w tryb aktywacji przy warunku pomiar >= wartość zadana, określają czy zadany próg alarmowy został przekroczony. W momencie przekroczenia, aktywowane są markery M01, M02 oraz M03.
Ilustracja nr 4 pokazuje realizację kontroli wartości pomiarowych z dwóch przetworników prędkości powietrza. Różnica w warunku wystąpienia alarmu polega na tym, że jest on aktywowany w momencie zajścia jednego z dwóch warunków. Komparatory G04 i G06 realizują funkcję pomiar >= wartość zadana natomiast komparatory G05 i G07 sprawdzają warunek pomiar <= wartość zadana.
Rozwiązanie takie powoduje aktywację alarmu w momencie gdy pomiar znajdzie się poza określonym przedziałem (aktywowane są wówczas markery M04 i M05). Należy zwrócić uwagę na numerację wejść analogowych. Jak widać na powyższych zrzutach ekranowych, komparatory dotyczą wejść A01, A05, A06, A07 oraz A08.
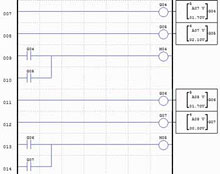
Ilustracja nr 4
Pierwsze z wejść jest kanałem dostępnym na jednostce centralnej, natomiast pozostałe dotyczą analogowego modułu rozszerzeń. Różne jednostki centralne mogą mieć różną ilość wejść analogowych, dlatego też cztery pierwsze są zarezerwowane. Wnioski z przeanalizowanego kawałka kodu źródłowego są następujące: w momencie przekroczenia poziomu alarmowego dla danego kanału pomiarowego, aktywowany jest odpowiedni marker Mxx.
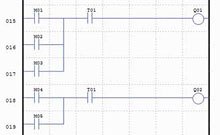
Ilustracja nr 5
Ilustracja nr 5 pokazuje fragment kodu odpowiedzialnego za aktywację przekaźnika alarmowego w momencie zaistnienia sytuacji alarmowej. Przekaźniki podłączone są do niskonapięciowych sygnalizatorów, które poza główną kolumną sygnalizacyjną informują operatora o wystąpieniu alarmu. Warto zwrócić uwagę na cewki timerów T01 oraz T02, które powodują przerywanie sygnału napięciowego dochodzącego do sygnalizatorów – powoduje to ich pulsację, co dodatkowo wpływa na szybkość reakcji operatora. Ostatni fragment kodu źródłowego (ilustracja nr 6) realizuje inicjację ekranów pomocniczych na wyświetlaczu sterownika (H01 i H02), inicjacje instrukcji czasowych (T01 i T02) oraz obsługę alarmu czasowego aktywującego kolumnę sygnalizacyjną (Q03).
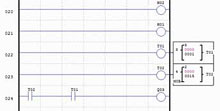
Ilustracja nr 6
Po upłynięciu czasu 15 minut, kolumna zaczyna pulsować zgodnie z przerwaniem czasowym. Wspomniane ekrany pomocnicze zostały zaprojektowane po to, aby operator mógł podejrzeć wartości pomiarowe bezpośrednio z poziomu sterownika (ilustracja nr 7). Jest to pomocne przykładowo w sytuacji awarii panelu operatorskiego.
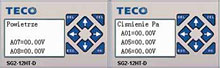
Ilustracja nr 7
Panel operatorski
Wizualizacja przeznaczona na dotykowy panel operatorski zrealizowana została w taki sposób, aby była jak najbardziej przejrzysta oraz cechowała się intuicyjną obsługą. Projekt ekranu startowego pokazany został na ilustracji nr 8.
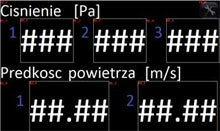
Ilustracja nr 8
Widzimy zatem kontrolki odpowiedzialne za wyświetlanie odpowiednich wartości pomiarowych. Przypisanie danej kontrolki do odpowiedniego rejestru danych w sterowniku, realizowane jest w momencie dwukrotnego kliknięcia na nią. Pojawi się wówczas okno pokazane na ilustracji nr 9 (poniżej).
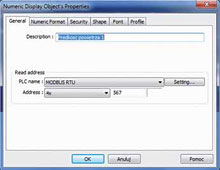
Ilustracja nr 9
Jest to okno konfiguracyjne kontrolki odpowiedzialnej za wyświetlanie pomiaru prędkości przepływu. Programista musi określić interfejs komunikacyjny (MODBUS RTU), który sparametryzowaliśmy wcześniej (ilustracja nr 2) i wybrać konkretny typ oraz numer rejestru danych. Lista rejestrów sterownika wraz z przyporządkowanymi adresami dostępna jest razem z instrukcją obsługi urządzenia. Dokładnie w ten sam sposób parametryzowane są pozostałe pomiary i wskaźniki. Na ekranie dodane zostały niewidzialne podczas poprawnej pracy systemu kontrolki bitowe, odpowiedzialne za podświetlanie pomiaru na czerwono w momencie wystąpienia alarmu na odpowiednim kanale pomiarowym. Przykładowa konfiguracja pokazana została na ilustracji nr 10 (poniżej).
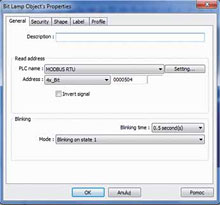
Ilustracja nr 10
W miejscu, w którym konieczne jest określenie rejestru danych, wybrane zostały opisane wcześniej markery M01-M05, których aktywacja w sterowniku jednoznacznie identyfikuje alarm na konkretnym kanale. Projekt okna umożliwiającego modyfikacje parametrów progów alarmowych pokazany został na ilustracji nr 11.
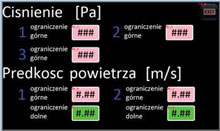
Ilustracja nr 11
Przypisanie kontrolek do adresów odpowiednich komparatorów w sterowniku realizowane jest podobnie jak wyżej. W trakcie pracy systemu, przy każdorazowej zmianie tych wartości w panelu, modyfikowane są progi w sterowniku. Modyfikacja ta dotyczy wartości zadanych w poszczególnych komparatorach. Należy zwrócić uwagę na ewentualne powtórne ładowanie programu do sterownika, gdyż podczas tej operacji wszystkie progi przywracane są do wartości domyślnych.
W takiej sytuacji, należy ponownie sparametryzować cały system. Panel operatorski został wyposażony w jeszcze jedną funkcję. Co 15 minut, sterownik wystawia sygnał na cewkę kolumny sygnalizacyjnej. Aby go skasować, wystarczy dotknąć ekran panelu w dowolnym miejscu. Zostało to zrealizowane poprzez przezroczysty przycisk binarny, kasujący znacznik przypisany do resetowania timera T02. Konfiguracja timera w sterowniku oraz przycisku w panelu, przedstawione zostały na ilustracji nr 12 oraz nr 13.
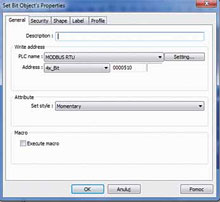
Ilustracja nr 13
PODSUMOWANIE SZKOLENIA
Wydaje się, że szkolenie to, wraz z poprzednim, w znacznym stopniu wyczerpały problem integracji systemów bazujących na sterowniku SG2. W trakcie 5 kolejnych szkoleń pokazana została mnogość możliwości zastosowania tych sterowników z urządzeniami innych producentów. Każdy system rozpatrywany musi być indywidualnie i w taki właśnie sposób projektowany. Jednakże wiedza zdobyta w czasie tego kursu powinna być wystarczająca aby poradzić sobie z większością problemów programistycznych. W kolejnych wydaniach „Pod kontrolą” z pewnością znajdą się nawiązania do tego tematu.
autor:
Dominik Szewczyk
dszewczyk@introl.pl