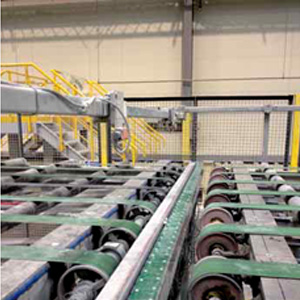
We wcześniejszych wydaniach magazynu Pod Kontrolą (28/2014 i 34/2015) były opisywane najczęściej stosowane metody pomiaru wilgotności materiałów sypkich. Przedstawione metody umożliwiały pomiar w różnych aplikacjach i dla różnych wymagań Użytkownika. Wspólną cechą wszystkich metod było to, że pomiar był realizowany w miejscu zainstalowania sensora, a więc uzyskiwana informacja odnosiła się do niewielkiej części produktu. W niektórych sytuacjach to za mało, bo dla właściwego prowadzenia procesu produkcji potrzebny jest szerszy obraz. Czy można go uzyskać?
SENSOR POJEMNOŚCIOWY I WARUNKI JEGO STOSOWANIA
Ta szczególna informacja ma znaczenie przy wytwarzaniu produktów w postaci płyt, płytek czy taśm. Nie można ich z pewnością nazwać „produktami sypkimi”, jednak ze względu na specyficzne warunki aplikacji, możliwe jest zastosowanie do pomiaru ich wilgotności metody pojemnościowej. Metoda ta jest metodą pośrednią i polega na pomiarze pojemności elektrycznej „kondensatora” utworzonego przez sensor pomiarowy oraz badany produkt. Zmiany pojemności kondensatora wynikają ze zmian wilgotności produktu. Przypomnijmy sobie, że woda ma wysoką stała dielektryczną (ok. 80) w porównaniu z innymi materiałami, więc jej obecność silnie wpływa na wypadkową stałą dielektryczną. Im większa zawartość wody w mierzonym produkcie, tym stała dielektryczna wyższa, im materiał bardziej suchy, tym niższa stała dielektryczna. Ponieważ zazwyczaj wiedza na temat właściwości dielektrycznych produktu nie jest użyteczna, konieczne jest określenie korelacji między wypadkową stałą dielektryczną, a wilgotnością.
Służy temu proces kalibracji, podczas którego wskazaniom sensora pojemnościowego przyporządkowuje się odpowiednie wartości wilgotności zmierzonej metodą laboratoryjną (referencyjną). Dzięki przeprowadzeniu kalibracji Użytkownik może mierzyć wilgotność produktu w sposób ciągły, bez konieczności pobierania próbek i prowadzenia czasochłonnych pomiarów w laboratorium.
Przy tak realizowanym pomiarze istnieje jedno ważne założenie – zmiany zawartości wody są jedynym czynnikiem wpływającym na zmiany pojemności „kondensatora”. Nie mogą zatem zmieniać się rozmiary „kondensatora” (czyli ilość produktu będącego w zasięgu sensora), ani rodzaj i właściwości dielektryka wypełniającego „kondensator” (mierzy się zawsze ten sam produkt, o tej samej gęstości, składzie itd.). Można zauważyć, że w przypadku takich produktów jak płyta kartonowo-gipsowa, płytka ceramiczna czy bloczek gipsowy, przy zachowaniu zaleceń odnośnie umiejscowienia i montażu sensora, wymienione wyżej warunki są spełnione (Rys. 1.).
Dodatkowo sensor nie musi się stykać z produktem i pomiar odbywa się bezkontaktowo. Może się zdarzyć, że na tej samej linii produkowane są płyty o różnej grubości lub bloczki z różnych materiałów, ale w takiej sytuacji wystarczy przeprowadzić kalibrację sensora dla każdego produktu i później stosować odpowiednio zapamiętane krzywe kalibracyjne.
MATRYCA SENSORÓW I OPROGRAMOWANIE
Punktowy pomiar wilgotności jest podstawowym elementem systemu mierzącego jej rozkład. Jak wspomniano we wstępie, pomiar wilgotności (także za pomocą sensora pojemnościowego) ma ograniczony zasięg. Zatem dla uzyskania „szerszej” informacji konieczne jest zastosowanie większej ilości sensorów zainstalowanych w odpowiedni sposób. Pojedynczy sensor ma rozmiar 50 x 50 mm. Ilość sensorów należy dobrać odpowiednio do szerokości mierzonego elementu lub szerokości przenośnika np. dla przenośnika rolkowego o szerokości 2500 mm buduje się układ składający się z 50 sensorów. Czujniki są montowane na specjalnej listwie i razem tworzą matrycę pozwalającą na pomiar rozkładu wilgotności w całym przekroju badanego elementu (Rys. 2.).

Rysunek 2. Matryca sensorów zainstalowana na przenośniku rolkowym
Informacja o rozkładzie wilgotności (Rys. 3.) wzdłuż szerokości elementu jest najczęściej niewystarczająca. Interesujący jest jej rozkład na całej powierzchni płyty. Aby uzyskać taką wiedzę należy w sposób ciągły rejestrować dane dostarczane przez wielopunktowy sensor wilgotności. Jest oczywiste, że ilość zgromadzonej w ten sposób informacji jest olbrzymia i dla jej przeanalizowania oraz zaprezentowania w czytelny sposób niezbędny jest specjalny software. Oprogramowanie prezentuje dane w formie graficznej, w sposób pozwalający na łatwe ocenianie jakości produkowanych elementów, a także wyciąganie wniosków co do potrzebnych korekt w ustawieniach procesu produkcyjnego.

Rysunek 3. Informacja z matrycy sensorów – wilgotność w przekroju poprzecznym dla 2 płyt
SYSTEM IMPS W TEORII I PRAKTYCE
Opis sposobu działania, budowy oraz instalacji odnosi się do systemu IMPS-4400 firmy Sensortech. System ten jest stosowany wszędzie tam, gdzie produkt ma postać płyty (np. płyta wiórowa, płyta MDF), a w szczególności płyty o niejednorodnej budowie (płyta kartonowo-gipsowa). Zalety pomiaru pojemnościowego, wykorzystywanego przez system IMPS są widoczne zwłaszcza w tym ostatnim przypadku. Warstwowa budowa płyty powoduje, że wilgotność nie rozkłada się wewnątrz płyty w sposób jednorodny – inny jest rozkład wilgotności w zewnętrznych warstwach kartonu, a inny w wewnętrznej warstwie gipsu. Sensory systemu IMPS zawsze mierzą wilgotność całkowitą, zawartą w całej objętości płyty. Inne urządzenia, jak sensory NIR, czy systemy wykorzystujące kamery termowizyjne, mają możliwość badania wilgotności jedynie na powierzchni płyty. Uzyskana za ich pomocą informacja może być użyteczna tylko przy założeniu, że znana jest korelacja między wilgotnością całkowitą, a powierzchniową. Nie zawsze jednak taka sytuacja ma miejsce.
Jak już wspominałem, system IMPS jest stosowany najczęściej na liniach do produkcji płyt kartonowo-gipsowych, gdzie końcowym etapem procesu produkcji jest suszenie płyt. Płyty są umieszczane w suszarni na półkach (od 8 do 16 poziomów), na których odbywają całą drogę od wejścia do wyjścia.
Wieloelementowy sensor wilgotności systemu IMPS jest montowany na przenośniku rolkowym, którym są transportowane wszystkie płyty opuszczające suszarnię. Kolejność rozładunku półek może być różna, dlatego dodatkowym elementem systemu IMPS są detektory podające, z której półki dana płyta pochodzi. Wszystkie informacje zgromadzone w systemie dokumentują jakość każdego wyprodukowanego elementu – zapisane są data i czas produkcji, numer półki w suszarni oraz obraz rozkładu wilgotności na całej powierzchni płyty. Kontrola jakości może w każdej chwili sprawdzić dane odnośnie dowolnej płyty, która opuściła linię produkcyjną.
OPTYMALIZACJA SUSZENIA
Analiza danych dostarczanych przez system IMPS pozwala także na wyciągnięcie wniosków odnośnie pracy samej suszarni. Rozkład wilgotności dla poszczególnych płyt pokazuje (Rys. 4.), w jaki sposób powietrze suszące przepływa przez suszarnię, jak rozkładają się przepływy w strefie środkowej i strefach bocznych, a także jak wyglądają przepływy na poszczególnych półkach.

Rysunek 4. Rozkład wilgotności na powierzchni 2 płyt
Doświadczony operator może w odpowiedni sposób dobrać ustawienia wentylatorów tłoczących gorące powietrze oraz zmienić ustawienie klap rozprowadzających powietrze na półkach. Operacje te mają na celu uzyskanie jednorodnego rozkładu wilgotności na wszystkich płytach, niezależnie od drogi jaką przebywają podczas suszenia. Jeżeli w wyniku zmiany ustawień nastąpi wyrównanie wilgotności płyt, będzie można przejść do kolejnego kroku optymalizacji polegającego na obniżeniu temperatury powietrza służącego do suszenia. Badania prowadzone wśród producentów amerykańskich wykazały, że obniżenie temperatury o 8 stopni w stosunku do poziomu utrzymywanego wcześniej, dają w ciągu roku oszczędności pozwalające na pokrycie kosztów zakupu systemu IMPS!
PODSUMOWANIE
Na zakończenie warto przypomnieć najważniejsze korzyści, jakie uzyskuje się w wyniku jego zastosowania. Podstawowym zadaniem systemu jest dostarczanie pełnej informacji na temat rozkładu wilgotności w każdym produkowanym elemencie. Dzięki systemowi Dział Kontroli Jakości ma dostęp do wszystkich danych zarejestrowanych na serwerze, zmniejsza się ilość elementów nie spełniających wymagania specyfikacji produktu, zmniejsza się także zużycie energii niezbędnej do suszenia.
Nasze doświadczenia oraz doświadczenia naszych zagranicznych partnerów wskazują, że typowy czas zwrotu z inwestycji w system IMPS wynosi około 12 miesięcy.