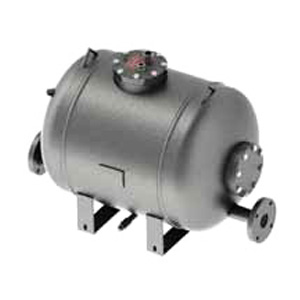
Zmieniający się klimat, rygorystyczne przepisy środowiskowe, podwyższanie standardów bezpieczeństwa, równoważenie popytu i podaży i oszczędności energetyczne, to główne wyzwania w dzisiejszym świecie przemysłowym. Wyzwania te w szczególności dotyczą dużych zakładów takich jak rafinerie czy zakłady chemiczne. Przemyślana polityka zarządzania energią stanowi klucz do ich dalszego rozwoju, stąd też w niniejszym artykule weźmiemy pod lupę optymalizację systemów parowych, powietrza oraz powrotu kondensatu. Postaramy się przedstawić najczęściej pojawiające się problemy w branży przemysłowej, poszukamy rozwiązań i oszczędności energetycznych.
TURBINA
Zacznijmy od niezaprzeczalnego faktu. Zakłady chemiczne i rafinerie są niezależne energetycznie, same wytwarzają energię poprzez spalanie naturalnego paliwa i same ją rozprowadzają. Sercem procesu wytwarzania energii stanowi turbina, która jest elementem krytycznym. Do jej pracy niezbędne jest dostarczenie pary przegrzanej, bez jakichkolwiek drobinek wody. Jej łopatki obracają się bowiem z tak zawrotną prędkością, że najdrobniejsza wilgoć może spowodować ich uszkodzenie. Kluczową rolę stanowią więc odwadniacze, które mają za zadanie odprowadzić potencjalny kondensat. Specjalnie dla aplikacji pary przegrzanej stworzono odwadniacze bimetaliczne.

Odwadniacze bimetaliczne
Stosując je na odwodnieniu turbiny niezbędne jest zwrócenie uwagi, by w przypadku ewentualnej awarii, pozostały w pozycji otwartej. Skoro odwodnienie turbiny to tak newralgiczne miejsce, warto pomyśleć o stałym monitorowaniu pracy odwadniacza i przeanalizować jak często remontujemy turbinę i jak zabezpieczamy ją w razie uszkodzenia odwadniacza. Warto także zadać sobie pytanie: czy jesteśmy pewni, że odwadniacz właśnie w tej chwili pracuje sprawnie?

Monitorowanie odwadniacza
Jeżeli mamy co do tego wątpliwości, warto rozważyć stosowanie urządzeń, które zrobią to za nas. Stosunkowo niedawno na rynku pojawiła się nowa, bezprzewodowa technologia monitorowania odwadniaczy, która skutecznie ocenia ich działanie poprzez pomiar parametrów roboczych i ultradźwięków. Natychmiastowe powiadamianie o nieprawidłowościach wynikających z ewentualnego uszkodzenia, zablokowania lub przepuszczania pary pomoże zminimalizować straty produkcyjne oraz zmniejszy zużycie energii. Ponadto otrzymując komunikat o wadliwie działającym odwadniaczu w miejscach kluczowych takich jak turbina, służby odpowiedzialne za utrzymanie ruchu mają możliwość błyskawicznej reakcji. Każdy bowiem wie, że naprawa turbiny to olbrzymie obciążenie budżetu dla każdego zakładu, dlatego dobrą praktyką jest zdalna kontrola odwadniaczy w tak kluczowych miejscach.

Bezprzewodowy system monitoringu
ODWADNIANIE UKŁADÓW WYMIENNIKOWYCH
Zakłady chemiczne i rafinerie wytwarzając potężne ilości pary wodnej wyposażone są w tysiące odwadniaczy. Nie da się tego porównać do żadnej innej gałęzi przemysłu. To oczywiście kolejne wyzwanie dla jednostek utrzymujących pracę obiektu w należytym porządku. Monitorowanie, serwisowanie i stałe przeglądy są niezwykle istotne, gdyż każde uszkodzenie odwadniacza stanowi potencjalne źródło strat energetycznych. W tym miejscu należy wrócić do podstaw, czyli do rzetelnego doboru odwadniacza dla danej aplikacji. W aplikacjach pary przegrzanej najbardziej popularnymi odwadniaczami są odwadniacze bimetaliczne.

Zdjęcie odwadniacza przepuszczającego parę wodną.
Z kolei w odwodnieniach pary nasyconej prym wiodą odwadniacze dzwonowe. Warto zatrzymać się przy tych drugich, gdyż cechy takie jak odporność na zabrudzenia czy uderzenia hydrauliczne, praca przy przeciwciśnieniu, czy długa żywotność to atuty, które wyróżniają odwadniacze dzwonowe wśród innych i sprawiają, że jest to pierwszy wybór w większości aplikacji.

Najpopularniejsze odwadniacze stosowane w rafineriach i zakładach chemicznych
W procesach przemysłowych wykorzystujących wymianę ciepła istnieje wiele możliwości optymalizacji.
W szczególności odnosi się to do problemów związanych z regulacją, zalewaniem i zapowietrzaniem wymienników oraz odprowadzaniem kondensatu przy zmieniających się parametrach. Korozja pojawiająca się w wymiennikach parowo-rurowych jest powszechna na całym świecie i może narazić nas na bardzo duże koszta naprawy. Aby ich uniknąć należy odprowadzać kondensat z wymiennika w sposób ciągły. Nie jest to wcale proste, gdyż zmieniający się stopień otwarcia zaworu regulacyjnego przed wymiennikiem może spowodować powstanie efektu stall (czyli ujemnego ciśnienia różnicowego). Korozja w tym przypadku nie stanowi jedynego zagrożenia, gdyż ujemne ciśnienie różnicowe może spowodować zalanie wymiennika, nierównomierny rozkład temperatur oraz powstawanie uderzeń wodnych.
Remedium na te problemy są odwadniacze pompujące, które w zależności od różnicy ciśnień pełnią rolę odwadniacza lub pompy kondensatu. Kolejnym problemem jest powstawanie mieszaniny powietrza i nieskondensowanych gazów z parą wodną. Para z łatwością się kondensuje, a gazy pozostają tworząc barierę dla wymiany ciepła (pamiętajmy, że powietrze jest doskonałym izolatorem).

Odwadniacz pompujący
W związku z tym zalecane jest stosowanie odpowietrzników termostatycznych, które zapewnią nam ciągłe odprowadzanie powietrza i gazów poza urządzenia wymiennikowe. Będąc przy odpowietrznikach warto rozważyć ich zastosowanie także w instalacjach cieczy. Oczywiście będą to odpowietrzniki mechaniczne. Godne polecenia są odpowietrzniki pływakowe wykorzystujące niezawodny układ zaworowy odwadniaczy dzwonowych. Ich praca jest na tyle efektywna, że znalazły one swoje zastosowanie w aplikacjach takich jak woda, ciekły azot czy benzyna.
SYSTEMY PODGRZEWANIA PARĄ WODNĄ
Rafinerie oraz zakłady chemiczne wytwarzają całą rzeszę produktów. Wiele z nich wymaga określonej temperatury, by przesłać je z punktu „A” do punktu „B”. W związku z tym stosuje się systemy grzewcze wykorzystujące parę, zwane popularnie parogrzejkami. Zasadniczo, swoje zastosowanie mają w trzech aplikacjach, tj. do zabezpieczenia systemu przed zamarzaniem, do utrzymania odpowiedniej lepkości produktów procesowych oraz do zabezpieczenia urządzeń technologicznych takich jak pompy, przetworniki, zawory regulacyjne itp. Konstrukcja systemu grzewczego jest bardzo prosta. Rurociąg przesyłowy podgrzewany jest rurociągiem parowym, który znajduje się wewnątrz rurociągu głównego. W zależności od wymagań, rurociąg przesyłowy może być wyposażony w jeden, dwa lub trzy rurociągi grzewcze. Ich usytuowanie uzależnione jest od orientacji rurociągu głównego. Oprócz prawidłowego doboru parogrzejek, niezwykle istotne jest właściwie zaprojektowany system rozprowadzania pary wodnej i skuteczne odprowadzanie kondensatu. To klucz w zapewnieniu odpowiedniej temperatury dla przesyłanego produktu. W takim przypadku, rewolucyjnym rozwiązaniem stały się kompaktowe rozdzielacze pary oraz stacje zbiorcze kondensatu. Ta innowacja przyniosła same korzyści począwszy od redukcji kosztów związanych z instalacją, przez łatwy dostęp i ograniczenie powstawania ewentualnych przecieków, skończywszy na zwiększeniu bezpieczeństwa personelu.
Ponadto układ pionowy sprawił ograniczenie wykorzystanej powierzchni. W stacjach zbiorczych kondensatu niezwykłym atutem okazały się odwadniacze montowane na konektorach wyposażonych w zawory tłoczkowe. Zachowanie wysokiej szczelności, brak konieczności izolacji, bardzo szybki czas wymiany odwadniaczy to olbrzymie oszczędności energetyczne.

Schemat instalacji podgrzewania parą
Dodatkowym atutem tego typu rozwiązań jest ograniczenie elementów zapasowych do minimum, gdyż cała stacja zbiorcza wyposażona jest w jeden i ten sam typ odwadniacza.
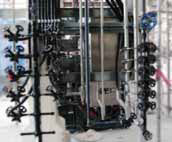
Rozdzielacz pary i stacja zbiorcza kondensatu
SYSTEMY POWIETRZA
Nie tylko optymalizacja systemów parowych przynosi ekonomiczne i środowiskowe korzyści. Kolejnym medium, które należy wziąć pod lupę jest powietrze. Zakłady produkcyjne przeznaczają sporo środków finansowych, by we wszystkich aplikacjach wykorzystujących powietrze, jego jakość była jak najwyższa. Niestety powszechne jest stosowanie powietrza zawierającego drobinki wody oraz niepożądane mikroelementy. Ten problem rozwiąże nam separator cyklonowy, który poprzez działanie siły odśrodkowej zapewni powietrze suche i czyste. Korzystajmy z niego w miejscach kluczowych oraz przed zaworami regulacyjnymi. Co więcej, rurociągi powietrza znajdują się na zewnętrznych instalacjach, podobnie zresztą jak rurociągi parowe. Ich lokalizacja sprawia, że straty energetyczne wynikające m.in. z kondensacji są częste i kosztowne. Rozwiązaniem tego problemu są przede wszystkim mechaniczne odwadniacze do powietrza. Montujmy je w najniższych punktach instalacji, na rozprowadzeniu powietrza i kompresorach. Pamiętajmy również o systematycznym badaniu szczelności instalacji, by wyeliminować powstające przecieki.

Separator cyklonowy
OPTYMALIZUJ, REDUKUJ, POPRAWIAJ
Optymalizowanie procesów energetycznych wymaga dużej wiedzy i doświadczenia, dlatego też warto czerpać ze sprawdzonych rozwiązań. Prawidłowa polityka utrzymywania wysokiej sprawności odwadniaczy na całym zakładzie, monitorowanie ich pracy w kluczowych miejscach to najlepsza droga do zminimalizowania strat energetycznych. Kolejnym ważnym elementem optymalizacji energetycznej jest odpowiednie zabezpieczenie urządzeń i powstającego produktu. Wymaga to niesłychanego wysiłku służb odpowiedzialnych za utrzymanie ruchu, jednak przy zachowaniu systematyczności w przeglądach i audytach, zmniejszymy częstotliwość przymusowych postojów i zyskamy dłuższą żywotność urządzeń.