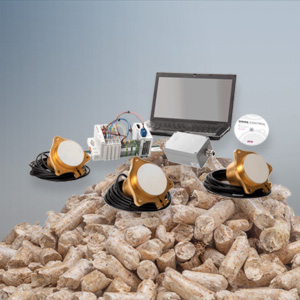
Biomasa – ten ogólny termin obejmuje głównie niekopalny materiał organiczny i biogenny, który z powodzeniem jest przetwarzany na energię (systemy grzewcze na biomasę). Pod pojęciem biomasy rozróżniamy między innymi trociny, zrębki, pelety drzewne, słomę itp. Rynek biopaliw, a zwłaszcza peletu, rozwija się dynamicznie od kilku lat w całej Unii Europejskiej, za sprawą przyjętej polityki, zwiększającej udział energii ze źródeł odnawialnych. Również w Polsce obserwowany jest dalszy wzrost zapotrzebowania na pelet, z roku na rok zwiększa się również ilość producentów tego paliwa. Szczególnie w branży peletów drzewnych, systemy pomiaru wilgotności firmy ACO stały się podczas produkcji niezbędne do oznaczania wilgotności w czasie rzeczywistym.
Granulki peletu posiadają dwa bardzo istotne, a przy tym wyróżniające czynniki, tj. atut zarówno ekonomiczny, jak i ekologiczny. Pelet drzewny jest bardzo czystym paliwem, nie zatruwa środowiska naturalnego, a do produkcji wykorzystywane są trociny i zrębki drzewne, tj. surowiec (odpad) praktycznie nie do wykorzystania gdzie indziej. Dzięki stosowanym przez producentów tego paliwa, nowoczesnym rozwiązaniom technologicznym i kontroli, produkcja nie jest uciążliwa dla środowiska naturalnego. Te aspekty nabierają dziś, w dobie rosnącej popularności ekologii oraz ograniczania emisji CO2 do środowiska, coraz większego znaczenia. Co niemniej ważne, biopaliwo (w tym pelet) jest również konkurencyjne cenowo w stosunku do węgla oraz oleju opałowego.
JAK POWSTAJE PELET?
Wyzwania jakim sprostać muszą producenci peletów to zmienne warunki pogodowe, sposób transportowania i składowania materiału (biomasy), a przede wszystkim efektywność procesu suszenia i wytłaczania trocin. Proces produkcji peletu odbywa się poprzez wtłaczanie suchych trocin lub zrębków drzewnych pod dużym ciśnieniem do dyszy formującej. Aby optymalnie prasować (wytłaczać) pelety, surowiec musi zawierać odpowiednią wilgotność – tę zaś, osiąga się poprzez suszenie lub kondycjonowanie (nawilżanie) surowego produktu. Zawarta w półprodukcie lignina, zmiękcza się wraz z powstałym w procesie ciepłem, to zaś przyczynia się do powstania bardziej zbitej struktury.

Rysunek 1. Schemat przedstawiający procesy przetwórstwa biomasy
PO CO MIERZYĆ WILGOTNOŚĆ PELETU?
Wysokiej jakości pelet o wysokich parametrach opałowych powinien posiadać jednorodną gęstość oraz wilgotność na poziomie nieprzekraczającym 10 %. Pomiar i kontrola wilgotności surowca do wyrobu peletu są kluczowe do tego, aby w końcowym etapie procesu otrzymać produkt o żądanej jakości.

Rysunek 2. Cyfrowy system pomiarowy DMMS
CYFROWY SYSTEM POMIAROWY DMMS
Jeśli zawartość wilgoci jest zbyt duża, uzyskanie produktu końcowego o żądanych parametrach może wymagać użycia większego ciśnienia w procesie kompresji. To z kolei powoduje niepotrzebny wzrost temperatury, generowanie zwiększonej ilości pary i zatykanie się dyszy. Uzyskany pelet może nie posiadać wymaganych parametrów opałowych i może istnieć ryzyko dekompozycji podczas dalszego składowania. Z kolei zatkanie dysz wymaga ręcznego czyszczenia przez operatora i powoduje uciążliwe przestoje podczas produkcji, generując straty. Jeśli zawartość wilgoci w surowcu jest za mała, proces kompresji produktu może nie być wystarczający i przy zbyt niskim ciśnieniu i temperaturze lignina nie zadziała odpowiednio efektywnie jako lepiszcze. Wówczas pelet nie uformuje się odpowiednio.
CZYM MIERZYĆ WILGOTNOŚĆ PELETU?
Tradycyjne metody pomiarowe wilgotności polegają na okresowych pomiarach na wagosuszarce przez operatora. Pomiary te jednak nie dają informacji na temat parametrów całości partii. Dodatkową wadą tego typu metod laboratoryjnych i ręcznych jest czas potrzebny na otrzymanie wyników pomiarowych, co wyklucza szybką reakcję na ewentualne błędne ustawienia parametrów linii i zwiększa możliwość powstania strat.

Rysunek 3. Kontaktowy czujnik wilgotności trocin we wnętrzu przenośnika ślimakowego

Rysunek 3. Kontaktowy czujnik wilgotności trocin we wnętrzu przenośnika ślimakowego

Rysunek 3. Kontaktowy czujnik wilgotności trocin we wnętrzu przenośnika ślimakowego
Tu właśnie wkraczają do akcji czujniki kontaktowe ACO, które mierzą wilgotność w czasie rzeczywistym i umożliwiają szybką i dokładną kontrolę procesu suszenia (lub nawilżania) do optymalnej wartości. Pomiar i kontrola parametrów procesu w czasie rzeczywistym jaki oferują rozwiązania ACO, zapewnia naszym Klientom poziom informacji o procesie niemożliwy do uzyskania dzięki innym sposobom. Wykorzystując system wilgotności DMMS uzyskujemy stały, dokładny i stabilny pomiar wilgotności w czasie rzeczywistym, który może posłużyć do kontroli i optymalizacji parametrów procesu. Kontaktowy czujnik pojemnościowy DMMS firmy ACO, mierzy i określa w czasie rzeczywistym zawartość wody (wilgoci) w produkcie, na podstawie różnicy stałej dielektrycznej odpowiednio dla produktu i wody. Zalecanym miejscem instalacji w procesie jest przenośnik ślimakowy – czujnik umiejscowiony jest w bocznej ściance przenośnika, w miejscu, w którym sonda ma stały kontakt z przemieszczającym się materiałem. Aby uniknąć zakłóceń sygnału powodowanych przez ruch samego przenośnika, praktykuje się skrócenie nieco najbliższej łopatki ślimaka do min. 3-4 cm od czujnika. Dobór odpowiedniego miejsca i wspomniana praktyka zalecanego skrócenia spirali jest praktykowana przez liczne zakłady produkcji peletu naszych klientów. Kluczowym aspektem jest również dokładna kalibracja układu pomiarowego, przeprowadzona po instalacji czujnika w miejscu docelowym i wykonana przy użyciu dedykowanego oprogramowania. Powinna ona uwzględniać siłę docisku i „ugniecenia” materiału dla zapewnienia jego stałej ściśliwości. Patrz rysunek 4. Przydatne miejsca, które z powodzeniem wykorzystują nasi klienci do montażu czujnika wilgotności to: – przed i za suszarką, – za silosem na wysuszone trociny, – na poziomie kondycjonowania (zwilżania), – bezpośrednio przed prasą – pelet za chłodnicą (gotowy produkt przed pakowaniem).

Rysunek 4. Kalibracja z wykorzystaniem dedykowanego oprogramowania
WILGOTNOŚCIOMIERZE SPRAWDZONE W PRAKTYCE
Dokładność jaką średnio uzyskujemy stosując kontaktowe czujniki wilgotności DMMS w realizacjach dla przetwórstw biomasy i produkcji peletu to ±0,5%. Oczywiście duży wpływ na finalny rezultat otrzymywanej dokładności pomiaru ma odpowiedni wybór miejsca usytuowania czujnika w procesie, jak również rzetelnie przeprowadzona kalibracja (z wykorzystaniem wagosuszarki). Otrzymane wyniki charakteryzują się bardzo dużą stabilnością i korelacją ze standardowymi, laboratoryjnymi metodami kontrolnymi. Zebrane dane mogą służyć automatyzacji i optymalizacji pracy suszarni, między innymi dozowaniu wody, optymalnego ustawienia czasu suszenia, czy sterowaniu pracą palników. W porównaniu z innymi metodami pomiaru wilgotności, czujniki kontaktowe firmy ACO charakteryzują się na najlepszym współczynnikiem otrzymywanej dokładności do ceny.

Rysunek 5. Przykłady pomiaru wilgotności peletu

Rysunek 5. Przykłady pomiaru wilgotności peletu
Do tej pory zainstalowaliśmy wiele takich systemów pomiarowych, które przyniosły i nadal przynoszą użytkownikom wymierne korzyści. Pomiar wilgotności peletu w czasie rzeczywistym zapewnia bowiem zwiększenie efektywności sterowania procesem, pożądaną powtarzalność i jakość produktu, obniżenie kosztów produkcji i zmniejszenie ilości odpadów. To w konsekwencji optymalizuje wydajność produkcji peletu, przy krótkim czasie zwrotu z inwestycji.