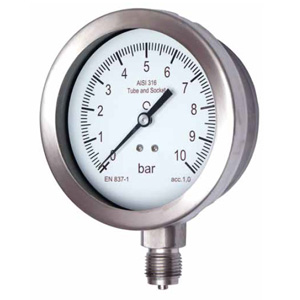
Jedną z najważniejszych wielkości, które należy kontrolować w procesach przemysłowych jest ciśnienie. Powszechnie wykorzystywanymi urządzeniami pomiarowymi w tym zakresie są manometry. Podobnie jak w przypadku każdego urządzenia pomiarowego, manometry muszą być wzorcowane w regularnych odstępach czasu, w celu upewnienia się, że zachowują swoje parametry metrologiczne. Przyjrzyjmy się 20 aspektom, które należy uwzględnić podczas wzorcowania manometrów.
MANOMETRY
Mówiąc o manometrach, zwyczajowo mamy na myśli analogowe wskaźniki ciśnienia wyposażone we wskazówkę i skalę ciśnieniową (choć oczywiście istnieją także manometry cyfrowe). Zazwyczaj są one wytwarzane zgodnie z normą EN 837 lub ASME B40.100. Często tego rodzaju analogowe manometry są zaprojektowane w oparciu o rurkę Bourdona, membranę lub puszkę. Mechaniczna konstrukcja powoduje wychylenie wskazówki na skali w miarę wzrostu ciśnienia. Manometry są podzielone na różne klasy dokładności, które określają dopuszczalny błąd pomiaru.
Dostępne zakresy ciśnienia są zazwyczaj uszeregowane krokowo o współczynnikach 1, 1.6, 2.5, 4, 6, następnie kontynuując dekadami (10, 16, 25, 40, 60) i tak dalej. Typowymi średnicami manometrów są zwykle 40, 50, 63, 80, 100, 115, 160 i 250 mm. Manometry o wyższej klasie dokładności mają większą średnicę.
WZORCOWANIE MANOMETRÓW – PODSTAWOWA ZASADA
Jeśli uprościmy zasadę wzorcowania pomiaru do minimum, to możemy powiedzieć, że podczas wzorcowania manometru porównujemy znany dokładny sygnał wejściowy z odczytanym wskazaniem na badanym manometrze, a następnie dokumentujemy i porównujemy wyniki. Różnica wartości jest błędem, a błąd powinien być mniejszy niż dopuszczalny błąd miernika (zwyczajowo zgodnie z klasą przyrządu).
1 – KLASA DOKŁADNOŚCI
Manometry są dostępne w wielu różnych klasach dokładności. Klasy dokładności są określone w normie EN 837 (klasy dokładności od 0,1 do 4% zakresu pomiarowego), jak również w standardzie amerykańskim ASME B40.100 (klasy dokładności od 0,1 do 5% zakresu pomiarowego). Najczęściej specyfikacja klasy dokładności „%” oznacza, że jeśli klasa dokładności wynosi 1%, a zakres skali wynosi od 0 do 100 kPa, to błąd wynosi ±1kPa. Upewnij się, że znasz klasę dokładności miernika, który zamierzasz wzorcować, ponieważ w naturalny sposób określa ona dopuszczalny poziom błędu, ale będzie to miało również inne skutki w procedurze kalibracji.
2 – MEDIUM
Podczas wzorcowania manometrów najczęściej stosowanym medium ciśnieniowym jest gaz lub ciecz. Zwykle jako gaz stosowane jest powietrze, ale w niektórych zastosowaniach mogą to być również inne gazy, takie jak azot. Jako ciecz przeważnie stosowane są woda lub olej. Zastosowane medium podczas kalibracji zależy od medium używanego w procesie, do którego podłączany jest manometr. Użyte medium zależy również od zakresu ciśnienia. W przypadku niskich zakresów pomiarowych do kalibracji najczęściej wykorzystywane jest powietrze/gaz, ale gdy zakres ciśnienia jest wyższy, bardziej praktyczne jest używanie cieczy jako medium.
3 – ZANIECZYSZCZENIA
Podczas kalibracji nie należy używać medium, które mogłoby spowodować problemy z ponownym zainstalowaniem miernika w procesie. Również sytuacja odwrotna nie jest wskazana tzn. czasami media procesowe mogą być szkodliwe dla sprzętu do wzorcowania. Wewnątrz miernika mogą znajdować się zanieczyszczenia, które dostając się do urządzeń kalibracyjnych spowodują szkody. Do manometrów pracujących z medium gazowym, można użyć pułapki zanieczyszczeń/wilgoci.
W przypadku manometru pracującego z medium cieczowym, należy go wyczyścić przed przystąpieniem do wzorcowania. Z jedną z najbardziej ekstremalnych sytuacji mamy do czynienia w przypadku miernika do pomiaru ciśnienia tlenu. Jeśli jakikolwiek smar lub tłuszcz dostanie się do wysokociśnieniowego układu tlenowego podczas wzorcowania miernika, cały proces może być bardzo niebezpieczny i spowodować eksplozję.
4 – RÓŻNICA WYSOKOŚCI
Jeśli urządzenie wzorcowe i wzorcowany manometr znajdują się na innej wysokości, ciśnienie hydrostatyczne mediów w rurociągach może powodować błędy. Zwykle nie jest to problemem, gdy jako medium stosuje się gaz, ponieważ jest on lekki w porównaniu z cieczą. Ale gdy jako medium jest używana ciecz, może ona powodować dodatkowe błędy ze względu na wywierane w układzie ciśnienie hydrostatyczne. Wielkość błędu zależy od gęstości cieczy i różnicy wysokości, ponieważ na ciecz oddziałuje siła grawitacji. Jeśli nie jest możliwe ustawienie kalibratora i manometru na tej samej wysokości, wówczas wpływ różnicy wysokości powinien zostać obliczony i wzięty pod uwagę podczas wzorcowania.
Ciśnienie hydrostatyczne oblicza się w następujący sposób:
Gdzie:
Ph = ciśnienie hydrostatyczne
ρ = gęstość cieczy (kg/m3)
g = lokalna grawitacja (m/s2)
h = różnica wysokości (m)
Na przykład: jeśli medium jest woda (gęstość 977,56 kg/m3), lokalna grawitacja wynosi 9,8 m/s2, a różnica wysokości pomiędzy wzorcowanym manometrem, a urządzeniem referencyjnym wynosi 1 m, to dodatkowy błąd wynosi 9,8 kPa (98 mbar). Przy tej okazji należy zauważyć, że w zależności od zakresu mierzonego ciśnienia, błąd spowodowany różnicą wysokości może być znaczący.
5 – TEST SZCZELNOŚCI
Jeśli podczas wzorcowania wystąpią jakiekolwiek nieszczelności w układzie, mogą one powodować nieprzewidziane błędy. Dlatego test szczelności należy wykonać przed kalibracją. Najprostszym sposobem przeprowadzenia testu jest zwiększenie ciśnienia w układzie i utrzymanie go przez pewien czas jednocześnie kontrolując, czy ciśnienie nie spada zbyt mocno. Niektóre systemy kalibracji (z wykorzystaniem regulatora ciśnienia, który zapewnia ciągłą regulację ciśnienia w układzie pomiarowym) mogą utrzymywać ciśnienie nawet w przypadku drobnych nieszczelności. W takim przypadku trudno jest zauważyć wyciek, więc kontroler powinien być zamknięty w trakcie przeprowadzania testu szczelności systemu. Zanim uznasz, że układ jest nieszczelny, sprawdź czy gwałtowna zmiana ciśnienia nie jest związana z efektem adiabatycznym.
6 – EFEKT ADIABATYCZNY
W zamkniętym układzie z gazem jako medium, temperatura gazu wpływa na objętość gazu, która z kolei ma wpływ na ciśnienie. Gdy ciśnienie gazu szybko wzrasta, powoduje to wzrost temperatury, natomiast wyższa temperatura powoduje, że gaz się rozszerza, a zatem ma większą objętość i wyższe ciśnienie. Gdy temperatura zacznie opadać, objętość gazu staje się mniejsza, co spowoduje spadek ciśnienia. Ten spadek ciśnienia może wydawać się wyciekiem w systemie, ale w rzeczywistości jest efektem adiabatycznym spowodowanym zmianą temperatury gazu (im szybciej zmienia się ciśnienie, tym większy jest efekt). Zmiana ciśnienia spowodowana tym efektem będzie stopniowo zmniejszać się wraz ze stabilizacją temperatury.
7 – UŻYCIE ODPOWIEDNIEJ SIŁY PRZY DOKRĘCANIU
W przypadku manometrów o dużej czułości na przyłożoną siłę, należy zachować szczególną ostrożność podczas dokręcania złączek do miernika, ponieważ może to spowodować jego uszkodzenie. Zawsze należy postępować zgodnie z instrukcjami producenta dotyczącymi dozwolonej siły dokręcania, używając przy okazji odpowiednich narzędzi, adapterów oraz uszczelek.
8 – POZYCJA MONTAŻU
Ponieważ manometry są instrumentami mechanicznymi, ich pozycja montażu ma wpływ na wskazywaną wartość. Dlatego zaleca się wzorcowanie manometru w tej samej pozycji, w jakiej jest używany w procesie. Należy również wziąć pod uwagę specyfikacje producenta dotyczące pozycji pracy. Typowo przyjmuje się, iż zmiana pozycji montażowej o 5° nie powinna zmieniać wskazań o więcej niż 0,5 jego klasy dokładności.
9 – ZADAWANIE CIŚNIENIA
W celu wywzorcowania manometru, należy przyłożyć źródło ciśnienia do miernika. Można to zrobić na różne sposoby: użyć ciśnieniowej pompki ręcznej, regulatora ciśnienia z butlą lub kalibratora obciążnikowo-tłokowego. Kalibrator obciążnikowo-tłokowy zapewni bardzo dokładne ciśnienie i nie wymaga osobnego kalibratora do pomiaru ciśnienia. Taki kalibrator jest jednak drogi, mało mobilny, wymaga dużej uwagi i jest wrażliwy na zabrudzenia. Z uwagi na to, do wzorcowania ciśnienia bardziej powszechne jest zastosowanie ręcznej pompki kalibracyjnej, najczęściej z noniuszem (do precyzyjnego nastawienia ciśnienia), za pomocą której zadajemy ciśnienie; oraz dokładnego urządzenia do pomiaru ciśnienia (kalibratora).
10 – WSTĘPNE ZADANIE CIŚNIENIA
W manometrze, ze względu na jego mechaniczną konstrukcję, zawsze będzie występowało tarcie w trakcie ruchu, co może zmieniać jego zachowanie z biegiem czasu. Właśnie dlatego przed kalibracją należy wstępnie zadać ciśnienie. Takie wstępne zadanie ciśnienia należy przeprowadzić zwłaszcza w przypadku, gdy miernik nie był przez pewien czas poddawany działaniu ciśnienia. W tym celu zadajemy maksymalne ciśnienie nominalne i pozostawiamy je na minutę, a następnie wypuszczamy i odczekujemy chwilę. Proces powtarzamy 2-3 razy przed rozpoczęciem właściwego cyklu kalibracji.
11 – ODCZYT MIERZONEJ WARTOŚCI (ROZDZIELCZOŚĆ)
Skala w analogowych manometrach ma ograniczoną czytelność. Posiada ona znaczniki skali głównej oraz pomocniczej, ale trudno jest dokładnie odczytać wartość ciśnienia, gdy wskazówka znajduje się pomiędzy znacznikami. Znacznie łatwiej dokonać odczytu, kiedy wskazówka znajduje się dokładnie na znaczniku skali. Dlatego zaleca się dostosować ciśnienie wejściowe tak, aby wskazówka znajdowała się dokładnie na znaczniku, a następnie zapisywać odpowiednie ciśnienie wejściowe. Działanie odwrotne, tj. podawanie dokładnego ciśnienia wejściowego w pierwszej kolejności, a następnie odczytanie wartości z manometru, spowoduje błędy wynikającej z ograniczonej dokładności odczytu.
Ważny jest również kąt pod jakim dokonywany jest odczyt wskazania na manometrze. Istotne jest aby dokonywać odczytu patrząc prostopadle do skali manometru. Wiele dokładnych manometrów ma za wskazówką usytuowane lustro wzdłuż skali. To lustro pomaga dokładnie odczytać wskazywaną wartość. Odczytu należy dokonywać tak, aby odbicie lustrzane wskazówki znalazło się dokładnie za rzeczywistą wskazówką. Wówczas wiadomo, że patrzymy prostopadle/prosto na manometr.

Niedokładności w odczycie wskazań manometru
12 – LICZBA PUNKTÓW WZORCOWANIA MANOMETRU
Różne klasy dokładności manometrów określają różną liczbę punktów wzorcowania. W przypadku najdokładniejszych manometrów (w klasie wyższej niż 0,05%), należy użyć „kompleksowej procedury kalibracji” i wykonać wzorcowanie w 11 punktach zakresu (punkt zerowy plus krok co 10% skali) w 3 cyklach góra/dół zadawania ciśnienia. W przypadku manometrów w średniej klasie (0,05% do 0,5%) należy zastosować „standardową procedurę kalibracji” z 11 punktami, ale z mniejszą ilości powtórzeń góra/dół. Mniej dokładne manometry (klasy 0,5% oraz gorszej) należy wzorcować za pomocą „podstawowej procedury kalibracji” z 6 punktami kalibracji (punkt zerowy plus krok co 20% skali) przy wzroście i spadku ciśnienia.
W praktyce manometry są czasami wzorcowane z mniejszą liczbą punktów wzorcowania. Oczywiście liczba punktów wzorcowania i cykli zależy również od wymagań aplikacji i dopuszczalnych błędów.
13 – HISTEREZA (KIERUNEK ZADAWANIA CIŚNIENIA)
Ponownie biorąc pod uwagę mechaniczną konstrukcję manometru, może on mieć pewną histerezę. Oznacza to, że wskazanie nie jest dokładnie takie samo, gdy porównamy ze sobą punkty wzorcowania w kierunku narastającym i opadającym ciśnienia. Aby dowiedzieć się, jaka jest wartość histerezy, należy przeprowadzić wzorcowanie manometru za pomocą rosnących i malejących punktów kalibracji, tzn. najpierw zadawać coraz większe wartości ciśnienia, a następnie zmniejszać ciśnienie. Robiąc to ważne jest, aby upewnić się, że zadajemy ciśnienie tylko w pożądanym kierunku. Na przykład podczas kalibracji przy użyciu coraz wyższych wartości ciśnienia, musimy upewnić się, że nie obniżymy ciśnienia w żadnym momencie podczas precyzyjnej regulacji ciśnienia, ponieważ spowoduje to utratę informacji o histerezie. Jeśli przekroczymy punkt docelowy wraz ze wzrostem ciśnienia, musimy obniżyć ciśnienie z powrotem, a następnie ponownie je podnieść do punktu docelowego.
14 – DELIKATNE STUKANIE W MANOMETR
Czasami mechaniczny manometr może wymagać delikatnego stuknięcia w celu upewnienia się, że nie jest on przyblokowany przez jakiekolwiek tarcie lub utratę elastyczności, szczególnie jeśli nie był użytkowany przez dłuższy okres czasu. Podczas wzorcowania, gdy ciśnienie wejściowe zostanie ustabilizowane, możesz delikatnie stuknąć w manometr, aby sprawdzić, czy wskazanie się zmieni. Oczywiście robiąc to należy być delikatnym, aby nie uszkodzić miernika.
15 – ILOŚĆ CYKLI KALIBRACJI (POWTARZALNOŚĆ)
Podczas wzorcowania cykle wzorcowania powtarza się kilka razy w celu określenia powtarzalności wzorcowanego przyrządu. Jeśli wzorcowany manometr ma złą powtarzalność, da różne wyniki podczas kolejnych cykli kalibracji. Jeśli wywzorcowany zostanie tylko jednym cyklem, tracimy informacje o powtarzalności. Jak wspomniałem wcześniej, najdokładniejsze manometry powinny być wzorcowane za pomocą 3 cykli. W praktyce powtarzalność jest często prowadzona jako badanie typu dla konkretnych instrumentów (marka/model). Gdy znana jest typowa powtarzalność, faktyczna kalibracja jest wykonywana tylko z jednym cyklem.
16 – ADIUSTACJA
Jeśli kalibracja wstępna (As Found) pokazuje, że manometr nie spełnia wymagań dokładności, należy coś zrobić. W większości przypadków wskaźnik powinien być tak ustawiony, aby mieścił się w dozwolonych granicach tolerancji. Po wyregulowaniu miernik należy ponownie poddać procedurze wzorcowania (As Left), aby zweryfikować stan, w jakim go pozostawiamy. Jeżeli nie jest możliwe przeprowadzenie adiustacji danego miernika, można obliczyć współczynnik korygujący i ten współczynnik należy wziąć pod uwagę przy normalnym użytkowaniu. To oczywiście utrudni użytkowanie manometru. Jeśli wskaźnik ma duży błąd, najlepiej go naprawić/wymienić, a nie próbować adiustować, ponieważ najprawdopodobniej nie będzie stabilny w przyszłości.
17 – DOKUMENTACJA – CERTYFIKAT KALIBRACJI
Ważnym aspektem wzorcowania jest oczywiście udokumentowanie wyników za pomocą certyfikatu kalibracji. Certyfikat powinien dokumentować zadawane ciśnienie i wskazanie badanego urządzenia oraz obliczenia błędu (różnicy przyłożonego ciśnienia i wskazania). Z pewnością certyfikat musi zawierać również inne informacje, zgodnie z normami/przepisami, w tym niepewność wzorcowania. Certyfikat można wypełniać ręcznie, tj. zapisywać wskazania miernika i wartości zadawanego ciśnienia na papierze, a następnie „ręcznie” obliczać błąd. Można również użyć zautomatyzowanego rozwiązania, które automatycznie wykona dokumentację i obliczenia, a także prześle wyniki do oprogramowania zainstalowanego na komputerze w celu wydrukowania wyników i archiwizacji.
18 – WARUNKI ŚRODOWISKOWE
Dla większości manometrów określono jaki wpływ na pomiar ma zmiana temperatury, co należy wziąć pod uwagę. Najczęściej manometr wzorcowany jest w temperaturze pokojowej, ale temperatura procesu może być zupełnie inna. Ta różnica temperatur między procesem a wzorcowaniem może powodować różnice w dokładności pomiaru. Warunki środowiskowe (temperatura i wilgotność) panujące w trakcie wzorcowania należy udokumentować w certyfikacie kalibracji.
19 – METROLOGICZNA IDENTYFIKOWALNOŚĆ
Podobnie jak w przypadku każdej kalibracji, należy upewnić się, że urządzenie referencyjne używane do wzorcowania manometru ma ważne własne świadectwo kalibracji, a jego kalibracja jest zgodna z odpowiednimi normami krajowymi (śledzenie metrologiczne).
20 – NIEPEWNOŚĆ WZORCOWANIA (TUR / TAR)
Podczas każdego wzorcowania należy zdawać sobie sprawę z całkowitej niepewności pomiarów kalibracyjnych, w przeciwnym razie wynik nie będzie miał dużej wartości. Świadomość znaczenia niepewności w zakresie kalibracji wydaje się wzrastać, a także jest coraz częściej uwzględniana w odpowiednich normach i przepisach. W niektórych obszarach zamiast obliczania niepewności stosuje się TUR (Test Uncertainty Ratio) lub TAR (Test Accuracy Ratio). Celem wyznaczenia tych współczynników jest upewnienie się, że posiadany kalibrator (lub wzorzec) jest kilka razy dokładniejszy niż przyrząd, który ma być wzorcowany, co pozwala na uniknięcie obliczania niepewności. Jednym z najczęściej używanych współczynników jest 1: 4, co oznacza, że specyfikacje kalibratora są czterokrotnie lepsze niż parametry wzorcowanego miernika.
W każdym razie dobrze jest zauważyć, że przy wykorzystaniu współczynników TUR/TAR, nie jesteśmy świadomi wszystkich istotnych składników niepewności w procesie kalibracji i nie wiemy, jak dobra jest kalibracja. Dlatego bardziej zalecane jest obliczenie niepewności standardowej (całkowitej).
PODSUMOWANIE
Jak widzicie Państwo po lekturze artykułu, jest przynajmniej 20 kluczowych kwestii jakie należy wziąć pod uwagę przy wzorcowaniu manometrów. Brak uwzględniania którejkolwiek może doprowadzić do niepoprawnego procesu wzorcowania, a co z tym związane, braku pewności co do wskazań swoich przyrządów. Z różnych względów postępowanie według tych 20 wytycznych może być utrudnione. Jednak czasami sama świadomość występowania pewnych zjawisk wystarczy do prawidłowej interpretacji wyników.