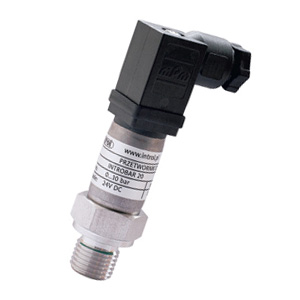
Ciśnienie, jako jedna z najpowszechniej mierzonych wartości w procesach przemysłowych, doczekało się wielu metod pomiaru i rozwiązań konstrukcyjnych. Obok urządzeń mechanicznych, których istota działania omawiana już była w jednym z numerów „Pod kontrolą” istnieją także urządzenia elektroniczne. Ich budowa, zasada działania oraz przeznaczenie są bardzo zróżnicowane, a ich prawidłowy dobór decyduje często o dokładności i stabilności prowadzonych pomiarów.
Do elektronicznych urządzeń pozwalających na kontrolę i pomiar ciśnienia w układach automatyki przemysłowej możemy zaliczyć zarówno te o bardzo prostej budowie, jak i te o zaawansowanych konstrukcjach i technologii przetwarzania sygnałów.
Do pierwszej grupy należą presostaty i przetworniki analogowe, drugą natomiast stanowią przetworniki inteligentne oraz manometry cyfrowe. Wszystkie te urządzenia niezależnie od stopnia zaawansowania technologicznego posiadają jedną bardzo ważną zaletę – pozwalają na przesyłanie informacji o mierzonym ciśnieniu w postaci sygnału analogowego bądź cyfrowego na większe odległości. Sygnał ten może być użyty do układów regulacji oraz wizualizacji procesów produkcyjnych. Możliwość przesyłania wyników pomiarowych do nadrzędnych systemów sterowania i monitoringu odróżnia elektroniczne od mechanicznych urządzeń pomiarowych, które wymagają odczytu w miejscu ich zainstalowania.
Trzy technologie pomiaru ciśnienia
Ze względu na materiał z jakiego wykonany jest sam czujnik pomiarowy oraz jego konstrukcję, elektroniczne urządzenia do pomiaru ciśnienia możemy podzielić na trzy podstawowe typy: tensometryczne, piezorezystancyjne oraz pojemnościowe.
Tensometr to drut oporowy, który na skutek przyłożonej siły poddawany jest odkształceniu, co wpływa na zmianę jego rezystancji. W przypadku czujników tensometrycznych drut ten naklejany jest na odpowiednie podłoże. Odkształcenia jakim podlegają tensometry powodują jednak bardzo małe, trudne do zmierzenia zmiany rezystancji. Dlatego w celu umożliwienia zmierzenia tak małych zmian, budowa tensometrycznych czujników do pomiaru ciśnienia oparta jest o mostek Wheatsona.
Wszystkie tensometry w mostku muszą posiadać taki sam opór i być przytwierdzone do powierzchni poddawanej działaniu ciśnienia w taki sposób, aby mostek znajdował się w równowadze. Rozmieszczenie tensometrów na powierzchni czynnej (poddawanej ciśnieniu) ma znaczący wpływ na czułość czujnika, co jest ich podstawową wadą. Jakość przytwierdzenia ma natomiast znaczący wpływ na samą dokładność pomiarów.
Zaletą tensometrów jest natomiast ich odporność na uderzenia i wibracje. Urządzenia te znakomicie nadają się przy tym do pomiarów dużych zakresów ciśnienia.
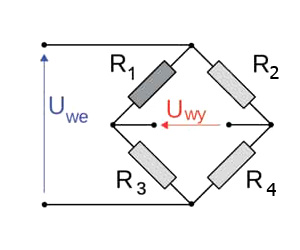
Mostek Wheatsona
R1 · R4 = R2 · R3
Warunek równowagi mostka
Na tej samej zasadzie działają najczęściej obecnie stosowane czujniki piezorezystancyjne.
W ich przypadku kawałek drutu oporowego oraz podłoże, na które jest naklejony, zastąpione zostały bardzo małych rozmiarów membraną krzemową rzędu mikrometrów z zaimplementowanymi rezystorami. Zakres pomiarowy jaki można uzyskać zależy od grubości membrany. Czujniki tego typu są znacznie dokładniejsze, posiadają większą stabilność długoterminową oraz czułość w stosunku do czujników tensometrycznych. Zaletą jest również możliwość pomiaru bardzo małych zakresów ciśnienia rzędu milibar.
Wadą tego typu czujników (podobnie jak tensometrycznych) jest duży wpływ temperatury na ich parametry. Czujniki piezorezystancyjne posiadają również małą odporność na wstrząsy i wibracje.
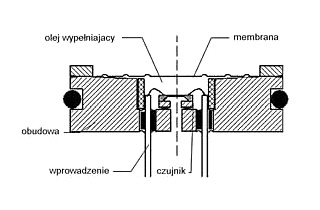
Cela pomiarowa z czujnikiem piezorezystancyjnym
Ostatnią grupą czujników są czujniki pojemnościowe, w których cienka membrana wykonana z krzemu znajduje się pomiędzy okładzinami, tworząc w ten sposób kondensator.
W wyniku przyłożonego ciśnienia zmianie ulega pojemność takiego kondensatora, co przekłada się na odpowiedni sygnał wyjściowy. Maksymalny zakres mierzonych ciśnień dla tego typu czujników to od 60 do 70 bar.
Dzięki swojej budowie, czujniki pojemnościowe wykazują większą stabilność długoterminową niż czujniki tensometryczne i piezorezystancyjne.
W celu ochrony przed niekorzystnym wpływem warunków środowiskowych czujniki umieszczane są w szczelnej obudowie. Obudowa wykonana jest ze stali nierdzewnej i wypełniona olejem silikonowym. Jednocześnie wyposażona jest ona w membranę o grubości rzędu mikrometrów, mającą bezpośredni kontakt z mierzonym medium.
Najczęściej membrana taka wykonana jest ze stali nierdzewnej. W trudnych aplikacjach, w których występuje np. wodór, membrana pokrywana jest cienką warstwą złota. Innymi materiałami wykorzystywanymi jako membrana pomiarowa są hastelloy, monel, tantal.
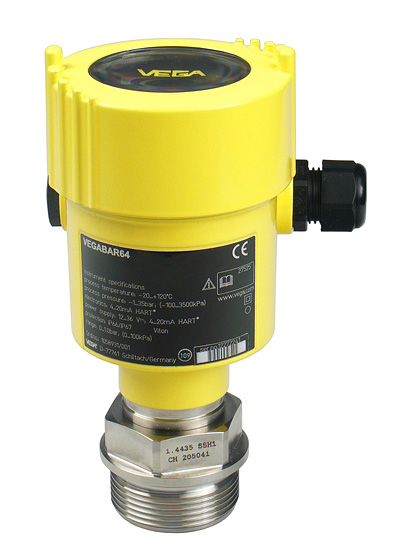
Vegabar 64
Często ze względu na wysoką temperaturę procesu konieczne jest zastosowanie odpowiedniego elementu chłodzącego. Może to być separator montowany bezpośrednio na przetworniku lub na kapilarze, czy też rurka impulsowa lub pętlicowa. W przypadku mediów lepkich, możemy zastosować przetwornik z płaską membraną, co zapewni łatwość czyszczenia i zapobiegnie oblepianiu.
Membrany takie umożliwiają uzyskanie równych powierzchni ze zbiornikiem, do którego są montowane. Znakomicie do tego celu nadają się przetworniki z membraną ceramiczną, w których jest ona automatycznie jedną z okładzin czujnika ciśnienia.
Uzyskujemy dzięki temu wysoką odporność na ścieranie i korozję, a sam czujnik może być przeciążony nawet do 150 razy.
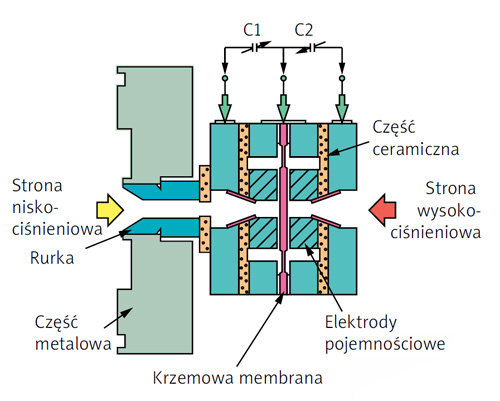
Cela pomiarowa z czujnikiem pojemnościowym
Proste vs inteligentne przetworniki pomiaru ciśnienia
Niezależnie od typu czujnika, elektroniczne urządzenia do pomiaru ciśnienia możemy również podzielić na dwie grupy ze względu na rodzaj sygnału wyjściowego. Do pierwszej grupy możemy zaliczyć proste przetworniki z analogowym, prądowym lub napięciowym sygnałem wyjściowym. Druga grupa to przetworniki inteligentne (z ang. smart sensor, intelligent transmitter), w których na wyjściu występuje sygnał cyfrowy.
W prostych przetwornikach do pomiaru ciśnienia, analogowy, wyjściowy sygnał pomiarowy podawany jest na układ wzmacniacza. Po wzmocnieniu, sygnał przechodzi przez właściwy przetwornik, który na wyjściu posiada sygnał użyteczny w przemyśle. Obecnie ze względów ekonomicznych (jedynie dwa przewody) oraz odporności na zakłócenia, stosuje się prądowy sygnał analogowy w postaci 4 … 20 mA (rzadziej sygnał napięciowy 0 … 10 V lub 0 … 5 V). Taki obwód wyjściowy nazywany jest pętlą prądową, w której przewody pomiarowe mogą równocześnie zasilać przetwornik. Wspomniany zakres sygnału wyjściowego jest proporcjonalnie rozłożony do zakresu pomiarowego przetwornika. Przykładowo, dla przetwornika o zakresie pomiarowym od 0 do 100 bar, prąd 4 mA odpowiada dolnej granicy ciśnienia czyli 0 bar, a górna granica ciśnienia 20 bar odpowiada prądowi 20 mA.
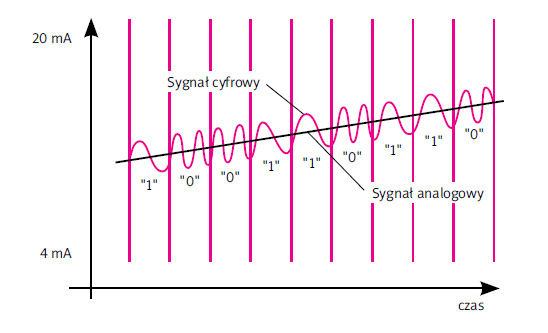
Sygnał Hart
Obecnie na rynku dostępne są również tzw. inteligentne przetworniki ciśnienia, w których w obwodzie pomiarowym, po wzmacniaczu, znajduje się przetwornik analogowo-cyfrowy oraz mikroprocesor. Przetwornik analogowo-cyfrowy odpowiada za zamianę analogowej wartości z czujnika pomiarowego na jego cyfrową wartość. Taki sygnał doprowadzony do mikroprocesora może być poddany dalszej obróbce. Umożliwia to między innymi skompensowanie wpływu temperatury na wynik pomiarowy.
Możliwa jest również konfiguracja poprzez np. zmianę zakresu lub ustawienie charakterystyki wyjściowej np. z liniowej na pierwiastkową lub jej inwersję. Umożliwiło to również wprowadzenie komunikacji cyfrowej pomiędzy przetwornikiem a systemem nadrzędnym, wykorzystując odpowiedni protokół komunikacyjny.
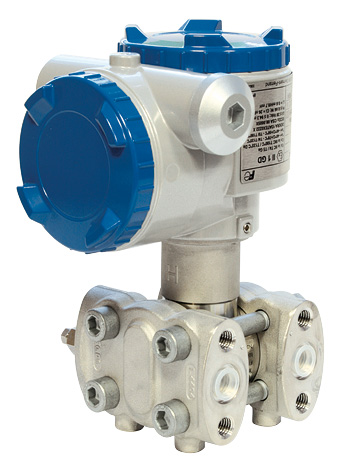
Inteligentny, pojemnościowy przetwornik ciśnienia
Współcześnie najpopularniejszym protokołem jest protokół Hart (Highway Addressable Remote Transducer), który został wprowadzony na rynek ponad 25 lat temu. Jest to protokół typu master-slave, w którym do jednego urządzenia nadrzędnego (master) możliwe jest podłączenie maksymalnie 15 przetworników będących urządzeniami podrzędnymi (slave).
Zwiększenie ilości podłączonych przetworników do jednej magistrali możliwe jest z wykorzystaniem nowszych protokołów komunikacyjnych takich jak Fieldbus i Profibus. Pozwala to na jeszcze większe oszczędności w okablowaniu.
W systemach typu Hart, Fieldbus i Profibus tylko jednostka nadrzędna może inicjować komunikację wysyłając zapytanie lub rozkaz do jednostki podrzędnej. W odpowiedzi master otrzymuje żądane dane, potwierdzenie wykonania rozkazu lub informację o powstałym błędzie. W Polsce protokół Hart wykorzystuje się głównie do konfiguracji i diagnostyki urządzeń.
W takim przypadku przetworniki z Hartem pracują jak prosty przetwornik z wyjściem analogowym, na którego sygnał 4÷20 mA nałożony jest sygnał cyfrowy, modulowany częstotliwościowo. Dzięki temu nie ma konieczności stosowania dodatkowego okablowania, a komunikator HART podpina się równolegle do istniejącego obwodu.
Kluczowe dopasowanie
Przy doborze odpowiedniego przetwornika ciśnienia konieczna jest znajomość procesu. Ma to kluczowe znaczenie między innymi dla wyboru odpowiedniego przyłącza procesowego. Nie możemy przykładowo zastosować przetwornika ciśnienia z przyłączem manometrycznym 1/2’’ dla procesów, w których występują wysokie temperatury lub medium posiada wysoką lepkość. Ważny jest też dobór samej membrany, a w zasadzie materiału z jakiego jest ona wykonana. Ma to duże znaczenie w przypadku pracy z mediami, których wpływ może mieć charakter destrukcyjny dla samego sensora. Należy również rozważyć typ sygnału wyjściowego przetwornika, gdyż nie ma potrzeby zakupu przetwornika inteligentnego w przypadku konieczności wysterowania jednego zaworu. Jednak w przypadku wystąpienia konieczności przeprowadzenia konfiguracji np. zmiany zakresu pomiarowego przetwornika ciśnienia, czy przekazywania sygnału do systemu nadrzędnego, zakup inteligentnego przetwornika ciśnienia jest jak najbardziej uzasadniony.
Wart zaznaczenia jest fakt, iż mimo rozwoju technologii elektronicznych urządzeń do pomiaru ciśnienia, wciąż bardzo dużo aplikacji wykorzystuje mechaniczne, odczytywane w miejscu pomiaru mierniki (np. manometry). Dzieje się tak oczywiście z uwagi na ceny urządzenie elektronicznych. W ostatnich czasach ich poziom znacząco się jednak obniżył, pozwalając na stopniowe zastępowanie urządzeń mechanicznych elektronicznymi. Szczególnie, że część producentów już pracuje nad udoskonalaniem swoich rozwiązań, z których chyba najbardziej praktycznym jest rozwój komunikacji bezprzewodowej. Pozwoliłoby to na dalszą oszczędność w zakresie okablowania oraz zwiększyło elastyczność planowania struktury zakładu produkcyjnego.