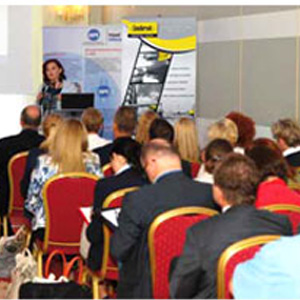
Śledząc poprzednie odsłony szkolenia dotyczącego tworzenia oprogramowania dla sterowników marki TECO, czytelnicy wielokrotnie mieli możliwość poznania praktycznego zastosowania opisywanych urządzeń w rzeczywistych aplikacjach użytkowych. W aktualnym numerze naszego kwartalnika, przedstawiony zostanie system transportu oraz segregacji paczek w jednej z firm sektora wydawniczego z okolic Warszawy.
ZAŁOŻENIA DOTYCZĄCE PROJEKTOWANEGO UKŁADU – PRZENOŚNIKI
Opisywany system sterowania dotyczył automatyzacji przenośników rolkowych, złożonych zarówno z długich odcinków napędzanych silnikami trójfazowymi wraz z motoreduktorami, jak i pojedynczych, stosunkowo krótkich sekcji zasilanych napięciem 24 VDC. Silniki 230 VAC wykorzystywane były do ciągłego transportu grupy paczek wzdłuż regałów magazynu, natomiast sekcje niskonapięciowe wszędzie tam, gdzie transportowane materiały musiały być zatrzymywane i segregowane pojedynczo. Taka konstrukcja zapewniała jednocześnie zakładaną funkcjonalność, szybkość działania, a także optymalizację kosztów inwestycji. Głównym wyzwaniem postawionym przed inżynierami naszej firmy była ocena możliwości integracji oraz sama integracja nowo projektowanego systemu ze starym, istniejącym już w docelowej lokalizacji. Ze względu na ewidentny podział układu na mniej i bardziej skomplikowany, stary system doskonale sprawdzał się na długim odcinku linii transportowej. Nowa część systemu, która dotyczyła segregacji paczek musiała zostać dobudowana w taki sposób, aby realnie zwiększyć efektywność całej aplikacji.
WAGA TOWAROWA
Oprócz samego systemu transportowego, aplikacja musiała zostać wyposażona w specjalnie układ tensometryczny, umożliwiający dokonanie dynamicznego pomiaru wagi każdej z transportowanych paczek. Przenoszonym asortymentem były książki różnej wielkości, posiadające różną, ale znaną wagę. Wielkość ta powinna umożliwiać weryfikację poprawnego załadunku każdej z paczek. W dalszej części artykułu opisany zostanie sposób porównywania wagi wzorcowej ze zmierzoną przez system decyzyjny. W zależności od tego procesu, system powinien podjąć automatyczną decyzję co do destynacji każdej z ważonych paczek.
OSTATECZNA KONSTRUKCJA SYSTEMU
Pierwszą częścią linii transportowej był wspomniany, długi przenośnik rolkowy, który został zaadaptowany ze starego systemu transportowego. Urządzenie napędzane było pięcioma silnikami z motoreduktorami, pracującymi w układzie trójkąta prądu trójfazowego. Ze względu na małe wymagania obciążeniowe, silniki sterowane były przy pomocy prostych falowników skalarnych firmy TECO. Kolejnym elementem systemu był odcinek odpowiedzialny za rozdzielanie „sklejonych” paczek, poprzez przyspieszanie każdej z kolejnych sekcji niskonapięciowych. Proces taki umożliwiał odpowiednie pokierowanie paczek wjeżdżających następnie na wagę. Sama konstrukcja układu wagowego zbudowana była z trzech przenośników taśmowych, spośród których kluczową funkcję pełnił środkowy – na nim odbywał się proces ważenia. Pozostałe dwa przenośniki realizowały odpowiednio przyspieszanie paczki do prędkości wagi oraz zwalnianie, aby ponownie dostosować prędkość do wartości nominalnej dla całej linii. W następnej kolejności paczka kierowała się do miejsca, w którym odbywała się realizacja podjętej decyzji dotyczącej akceptacji rzeczywistej wagi załadunku z wagą wzorcową. Jeżeli paczka została zrzucona, operator musiał ponownie przeprowadzić proces weryfikacji jej składu. W przeciwnym przypadku paczka kierowała się do strefy fakturowania, gdzie przy pomocy przenośników sekcyjnych, realizowany był proces akumulacji kartonów i rozdzielania zadań pomiędzy dostępne stanowiska wysyłkowe.
WYKORZYSTANIE STEROWNIKA TP03
Sterownik TECO TP03-60HR-A był odpowiedzialny za cały system transportowy. Zarówno falowniki napędzające wstępną linię przenośnikową, jak i przenośniki wagowe, a także wszystkie sekcje niskonapięciowe, sterowane były z jednej jednostki centralnej z dobudowanymi modułami wejść oraz wyjść cyfrowych (układ nie wymagał zastosowania sygnałów analogowych). Oprócz sterowania binarnego, najistotniejszym elementem była cyfrowa komunikacja z wykorzystaniem interfejsu RS485. Paczki były rozpoznawalne przy pomocy unikatowego kodu kreskowego, przyklejonego z boku każdej z nich. Wjeżdżając na wagę, kod był skanowany i przy pomocy protokołu znakowego przesyłany do sterownika (port COM1). Tam aktywowany był proces rozpoczęcia skanowania, weryfikacji zeskanowanego kodu, a następnie ważenia paczki i komunikacji z systemem bazodanowym (port COM2). Komputer nadrzędny zwracał do jednostki centralnej informację pozytywną lub negatywną i na tej podstawie paczka zostawała kierowana w odpowiednie miejsce. Poniżej znajdują się najciekawsze fragmenty rzeczywistego kodu odpowiedzialnego za proces decyzyjny wraz z komentarzami.
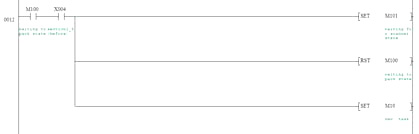
Rysunek 1: Oczekiwanie na kolejną paczkę
Cała konstrukcja systemu sterowania została oparta na mechanizmie maszyny stanów. W pierwszym z nich sterownik oczekuje na czujnik inicjujący rozpoczęcie procesu ważenia kolejnej paczki (wejście X004). Gdy sygnał się pojawi, sterownik przechodzi do kolejnego stanu.
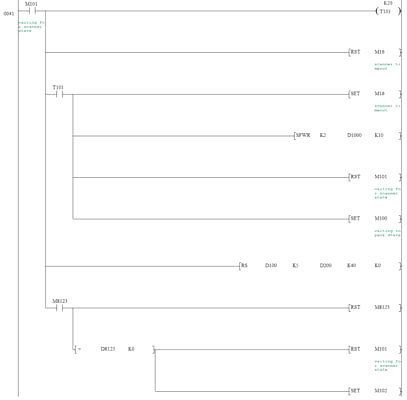
Rysunek 2: Oczekiwanie na skanowanie paczki
Po inicjacji procesu ważenia, system oczekuje na informacje dotyczącą identyfikatora paczki. W pierwszej kolejności aktywujemy czasomierz, który decyduje o upłynięciu czasu dozwolonego na zeskanowanie etykiety. Jeśli w zadanym okresie czasowym, skaner nie zwróci żadnej informacji, oznacza to, iż najprawdopodobniej miał miejsce błąd skanowania. Jest to równoznaczne z błędną wagą paczki (gdyż paczka bez kodu jest paczką niezweryfikowaną), więc system przechodzi do stanu początkowego (oczekuje na kolejną paczkę) i dodaje do kolejki wartość oznaczającą konieczność zrzucenia aktualnej na tor poboczny. Jest to realizowane poprzez polecenie SFWR – dodanie wartości do kolejki, która opróżniana jest każdorazowo w momencie aktywacji optycznego czujnika w miejscu zrzutu. Rozwiązanie takie umożliwia ciągłe skanowanie kolejnych paczek, bez konieczności każdorazowego czekania na zrzucenie poprzedniej paczki.
Jeżeli jednak paczka zostanie zeskanowana poprawnie i sterownik otrzyma transmisję ze skanera (warunek określany przez znacznik M8123), system przechodzi do kolejnego stanu, w którym sterownik ocenia wartość otrzymanych danych. Realizowane są porównania długości łańcucha znakowego z wartością zadaną, oraz porównywanie wybranych znaków z wzorcem. Jeżeli kod kreskowy w odniesieniu do tych warunków jest niepoprawny, sytuacja jest analogiczna jak w przypadku błędnej wagi – paczka musi zostać zrzucona. Jeżeli natomiast kod jest poprawny, system wysyła dane do komputera nadrzędnego. Tam następuje weryfikacja rzeczywistych danych pochodzących z wagi oraz pomiaru wzorcowego, odczytywanego każdorazowo z lokalnej bazy danych. W zależności od wyniku porównania, komputer wysyła zwrotne komunikaty „OK” lub „NOTOK” do sterownika.
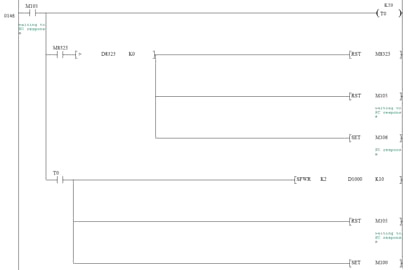
Rysunek 3: Oczekiwanie na odpowiedź komputera
Podobnie jak w przypadku oczekiwania na zeskanowany kod, sterownik aktywuje czasomierz albo móc zamknąć proces, jeżeli czas oczekiwania przekroczy zadaną wartość. Jeżeli jednak transmisja z komputera przebiegnie prawidłowo, sterownik przechodzi do procesu weryfikacji otrzymanej odpowiedzi. Weryfikacja polega na porównaniu każdego znaku odpowiedzi z wzorcem (OK w przypadku poprawnej wagi lub NOTOK jeżeli waga jest błędna). Aktywowane są odpowiednie markery, które określają poprawność pomiaru.
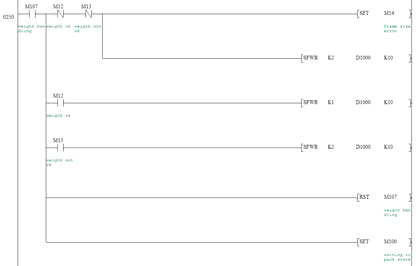
Rysunek 4: Ostateczna weryfikacja wagi paczki
Ostatni istotny stan sterownika to analiza tych markerów i uzupełnienie kolejki o wartości identyfikujące kolejne paczki poruszające się na odcinku od skanera do zrzutni. Należy zaznaczyć, że w zdecydowanej większości przypadków, kolejka jest uaktualniana dokładnie w tym miejscu, gdyż sytuacje zaniku pakietu danych lub braku odpowiedzi z komputera są bardzo rzadkie.
Analizując powyższy kod, można napisać, iż jeśli żaden z markerów nie jest aktywny, oznacza to błąd programu i zrzut paczki. Jeżeli waga paczki jest poprawna, wpisujemy do kolejki wartość 1, jeżeli niepoprawna- wartość 2. Uogólniając, wartość 1 oznacza pozwolenie na przejazd do strefy fakturowania, a wartość 2 – zrzut na boczny tor. Dlatego też każdy błąd procesu skanowania/ważenia kończy się wpisaniem wartości 2 do kolejki i rozpoczęciem procesu od początku. Ostatni istotny fragment programu to fragment dotyczący fizycznej realizacji zrzutu błędnej paczki. Został on przedstawiony na rysunku nr 5.
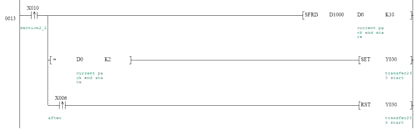
Rysunek 5: Realizacja decyzji dotyczącej zrzutu/przejazdu
Jeżeli paczka pojawi się w polu działania czujnika optycznego podłączonego do wejścia X010, system pobiera z kolejki najstarszy wpis i analizuje go pod względem zawartości. Jeżeli jest to liczba 2 oznaczająca jakikolwiek błąd, aktywowany jest przekaźnik wyjściowy uruchamiający silnik zrzutowy. Silnik zatrzymywany jest z momencie wykrycia markera indukcyjnego na pasku napędowym (aktywacja wejścia X006). Dzięki temu transfer wykonuje dokładnie jeden cały obrót i wraca do położenia początkowego, a paczka trafia na boczny tor. W przeciwnym wypadku, paczka spokojnie przejeżdża dalej do strefy fakturowania.
Na podstawie analizy opisanej aplikacji, można wyciągnąć wnioski dotyczące możliwych zastosowań sterownika TP03. Oprócz najbardziej typowych układów, w których sterownik pełni funkcję zbioru cyfrowych przełączników, uwydatniają się jego możliwości wykraczające poza podstawowe zastosowania. Doświadczenie płynące z analizy mnogości systemów, w których główna jednostką logiczną był właśnie sterownik TP03, pokazuje, iż ciężko wyznaczyć jakiekolwiek granice funkcjonalne tego urządzenia.