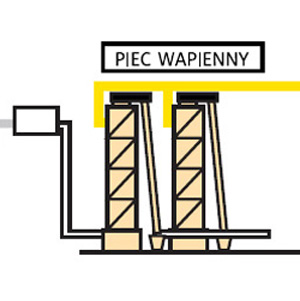
Słodki smak jest atrakcyjny dla człowieka od zawsze. Szacuje się, iż pierwszy cukier został wyizolowany około 3 000 lat przed naszą erą na terenach południowej Azji. Surowcem, z którego wytwarzano cukier była trzcina cukrowa rosnąca w regionach tropikalnych i subtropikalnych. Do połowy XVIII wieku trzcina cukrowa była jedynym źródłem cukru.
W roku 1747 niemiecki chemik Andreas Marggraf wyprodukował cukier z buraka cukrowego. Pierwsza cukrownia powstała w początku XIX wieku na Dolnym Śląsku, w miejscowości Konary. Od tego momentu kraje klimatu umiarkowanego przestały być zależne od importu cukru wytwarzanego z trzciny, a on sam stał się powszechnym artykułem spożywczym. Obecnie cukier stosowany jest praktycznie w całym przemyśle spożywczym, zarówno jako podstawowy surowiec do produkcji słodyczy, jak i dodatek niezbędny do uzyskania właściwego smaku lub regulator kwasowości.
Współcześnie surowcami do produkcji cukru na skalę przemysłową są trzcina cukrowa Saccharum officinarum (60% światowej produkcji) i burak cukrowy Beta Vulgaris (~ 40% światowej produkcji), a Polska zajmuje czołowe miejsce w Europie pod względem ilości produkowanego cukru. Przyjrzyjmy się jak w praktyce wygląda proces produkcji cukru z buraków i dlaczego analiza gazów jest w nim niezbędna.
ETAPY PRODUKCJI CUKRU
Współcześnie burak cukrowy uprawiany jest na masową skalę. Zebrane bulwy dojrzałych roślin dostarczane są do cukrowni, gdzie poddawane są obróbce. Przykładowy przebieg wytwarzania cukru z buraków cukrowych wygląda następująco:
1. Spławianie, oczyszczanie i mycie buraków
2. Otrzymywanie soku surowego
2.1. Krajanie buraków
2.2. Dyfuzyjne otrzymywanie soku dyfuzyjnego
2.3. Wysłodki i ich przerób (pasza)
3. Defekacja – oczyszczanie soku surowego
3.1. Wypalanie kamienia wapiennego i sporządzanie mleka wapiennego
3.2. Wstępne nawapnianie soku (defekacja wstępna)
3.3. Główne nawapnianie soku (defekacja główna)
3.4. Węglanowanie I (saturacja I)
3.5. Dekantacja i filtracja I soku węglanowanego
3.6. Węglanowanie II (saturacja II)
3.7. Dekantacja i filtracja II soku węglanowanego
3.8. Siarczynowanie soku rzadkiego
4. Zagęszczanie soku rzadkiego (stacja wyparek)
5. Krystalizacja cukru
5.1. Gotowanie cukrzycy I
5.2. Wirowanie cukrzycy I
5.3. Gotowanie i wirowanie cukrzyc II i III
5.4. Melas i jego dalszy przerób
6. Cukier biały (zaw. sacharozy >99.8%, wilgotność <0.08%, barwa biała, bez obcego zapachu).

Fragment schematu procesu technologicznego
Jednym z kluczowych etapów procesu technologicznego wytwarzania cukru jest defekacja, czyli oczyszczanie soku surowego. W procesie defekacji wykorzystywane jest mleko wapienne i gaz saturacyjny. Dolanie mleka wapiennego powoduje alkalizację soku i koagulację koloidów. W wyniku ogrzewania soku i poddania nawapnieniu głównemu (do pH 12–12,5) następuje rozkład związków przeszkadzających w uzyskaniu dobrej jakości cukru. Po defekacji głównej sok poddawany jest węglanowaniu (saturacji) w aparacie zwanym saturatorem, w którym przez słup soku przepuszcza się gaz saturacyjny. W soku tworzy się wówczas drobnokrystaliczna zawiesina węglanu wapniowego, który jest doskonałym pochłaniaczem dla niecukrów. Saturacja wiąże się z obniżeniem odczynu pH do wartości około 10,8-11,2. Mleko wapienne i gaz saturacyjny uzyskujemy przez wypalenie kamienia wapiennego. W wyniku termicznego rozkładu węglanu wapnia CaCO₃ uzyskuje się wapno CaO oraz gaz saturacyjny. Wapno następnie jest gaszone wodą i powstaje mleko wapienne, które wykorzystuje się do oczyszczania soku surowego.
GAZ SATURACYJNY
Gaz saturacyjny jest mieszanką dwutlenku węgla CO₂, tlenku węgla CO, tlenu O₂, azotu N₂, pary wodnej oraz zanieczyszczeń powstałych podczas pracy pieca wapiennego. Temperatura rozpatrywanej mieszaniny waha się w zależności od tego, który punkt instalacji jest rozpatrywany. Temperatura po płuczkach wodnych nie przekracza 40ºC, a ciśnienie 1 bara. Przykładowy – orientacyjny skład gazu saturacyjnego podawany w literaturze fachowej:
- dwutlenek węgla CO₂ – 30% … 40%
- tlenku węgla CO – 0,8% … 2%
- tlenu O₂ – 2% … 3%
- azotu N₂ – 50% … 55%
CELE PROWADZENIA ANALIZY GAZU SATURACYJNEGO
Ciągły pomiar nie tylko dwutlenku węgla, ale tlenku węgla i tlenu pozwala operatorowi pieca na szybkie podejmowanie decyzji prowadzących do optymalizacji pracy pieca wapiennego. Wysoki poziom CO a niski O₂ świadczy o zbyt małej ilości powietrza i niepełnym spalaniu (straty w koksie). Oba składniki wysokie to niewłaściwy przepływ powietrza przez warstwę wsadu w piecu (w części pieca niedomiar powietrza, a w innej nadmiar), to też straty paliwa.
Niska zawartość CO₂, CO i O₂ to najczęściej zbyt duża dawka koksu itd. Można tu rozpatrzeć jeszcze kilka wariantów, ale generalnie, znając w każdej chwili skład gazu możemy uniknąć strat w zużyciu kamienia (oprócz wapna mogą być niedopały i przepały), koksu, energii elektrycznej itp. Co ważne, w skrajnych przypadkach zbyt późna reakcja na wystąpienie niewłaściwego procesu wypalania kamienia wapiennego, może doprowadzić do trudności technologicznych w procesie oczyszczania soku i wręcz do ograniczenia produkcji.
Cele prowadzenia pieca wapiennego w skrócie:
- optymalizacja procesu spalania na podstawie pomiaru stężeń CO₂, CO i O₂,
- redukcja wpływu zjawisk takich jak:
– nieprawidłowy przepływ powietrza,
– niedomiar powietrza,
– niepełne spalanie, - ograniczenie zużycia koksu,
- zmniejszenie przepałów i niedopałów kamienia wapiennego,
- ograniczenie zużycia energii elektrycznej.
Znajomość parametrów gazu – przede wszystkim dwutlenku węgla (bo to on bierze udział w procesie saturacji) pozwala na bardziej precyzyjne sterowanie procesem. Najczęściej proces saturacji I przebiega w jednym kotle, lecz znane są także układy złożone z dwóch zbiorników. W obu przypadkach sterowanie ilością gazu jest od wartości pH w korekcie od ilości przepływającego soku. Zmiana stężenia CO₂ np. na skutek niedomknięcia górnego zamknięcia pieca wapiennego (dzwonu, lub klapy) powoduje, że układ odpowie z dużym opóźnieniem, co ma wpływ na końcową wartość pH. A od niej zależy czy nie będzie kłopotów z dekantacją soku i filtracją osadów – gęstwy I (zbyt wysokie końcowe pH) z jednej strony, bądź pogorszenia się efektu oczyszczania soków (przy przesaturowaniu następuje desorpcja niecukrów zaadsorbowanych na osadzie węglanu wapnia).
Dla II saturacji, której zadaniem jest pozostawienie minimalnej ilości rozpuszczalnych soli wapniowych w soku, odejście od optymalnego punktu pH (odpowiadające alkaliczności optymalnej) powoduje ich wzrost, czego następstwem jest zarastanie powierzchni grzejnych ogrzewaczy i aparatów stacji wyparnej oraz pogorszenie jakości otrzymywanego cukru (wzrost popiołu i mętności). Jak widać, znajomość składu gazu saturacyjnego pozwala na optymalizację procesu oczyszczania soku, który bezpośrednio wpływa na jakość procesu krystalizacji cukru (do systemów sterowania można wprowadzić korektę, szczególnie przy regulacji w proporcji od przepływu).
Dlaczego tak ważne jest prowadzenie Saturacji I i Saturacji II:
- właściwa ilość dostarczanego dwutlenku węgla w procesie karbonatacji wpływa bezpośrednio na jakość produkowanego cukru, redukuje:
– mętność,
– zawartość soli wapniowych,
– zawartość soli substancji nierozpuszczalnych. - redukcja zarastania powierzchni aparatów stacji wyparnej – ograniczenie zużycia energii cieplnej.
PO CO ANALIZOWAĆ GAZ SATURACYJNY?
Znajomość jakości gazu saturacyjnego jest ważna ze względu na poprawne prowadzenie pieca i procesu karbonatacji (saturacji) I i II. Optymalna zawartość dwutlenku węgla w gazie saturacyjnym umożliwia prowadzenie procesu saturacji bez zakłóceń (intensywne pienienie się soku w przypadku niskiej – ok. 25% zawartości CO₂).
- zawartość CO₂ (35-38%) – ciągły pomiar zawartości dwutlenku węgla decyduje o prawidłowym monitorowaniu pracy pieca wapiennego,
- zawartość CO (0,8-1,2%) – pomiar i rejestracja obrazuje poziom współczynnika nadmiaru powietrza przy spalaniu koksu oraz daje pełen obraz spalania koksu,
- zawartość O2 (1,5 – 2,0%) – jest wskaźnikiem szczelności pieca w górnej jego części oraz całej instalacji odbioru gazu z pieca. Tlen (jego ilość) decyduje o poprawności procesu spalania koksu.
Brak ciągłego pomiaru ww. gazów nie daje obsłudze możliwości szybkiej reakcji na zakłócenia w pracy pieca. Wiele zakłóceń udałoby się wcześniej wyeliminować, a ich skutki złagodzić, dzięki znajomości parametrów gazu. Oczywistym jest bowiem fakt, że prowadzenie procesu technologicznego o wysokim natężeniu przerobowym wymaga stabilnej zawartości gazu saturacyjnego, szybkiego reagowania i eliminowania zakłóceń u źródła (lub jeszcze z pewnym wyprzedzeniem). Co niemniej ważne, brak ciągłego analizatora gazu i opieranie się na wybiórczych (raz na zmianę) analizach gazu saturacyjnego (np. za pomocą aparatu Orsata), nie zapewnia pewności ruchowej pieca, poprawnej pracy wapniarni jako całości i stacji oczyszczania soku.
ANALIZA ONLINE = JAKOŚĆ + OSZCZĘDNOŚĆ
Ogólnie rzecz ujmując, analiza składu gazu i poprawna interpretacja zmierzonych wartości umożliwia uzyskanie produktu finalnego o wysokiej jakości, przy obniżeniu kosztów surowców i eksploatacji. Poprawne prowadzenie pieca wapiennego pozwala na zmniejszenie ilości zużywanego kamienia wapiennego, koksu i energii elektrycznej. Właściwa ilość dostarczanego dwutlenku węgla do procesu karbonatacji (saturacji I i II), wpływa na jakość produkowanego cukru – redukuje jego mętność, zawartość soli wapniowych i substancji nierozpuszczalnych.
Dodatkowo minimalizowane jest zarastanie powierzchni grzejnej aparatów stacji wyparnej, co ma bezpośredni wpływ na zużycie energii cieplnej. Jak widzimy, analiza składu gazu saturacyjnego ma niezwykle istotny wpływ na cały proces produkcji cukru, w szczególności na procesy saturacji I i II. Do analizy stosowane są specjalistyczne układy pomiarowe zbudowane przede wszystkim z analizatorów CO₂/CO , analizatorów O₂ i drogi gazowej. Takie układy pracują już w polskich cukrowniach, a szczegóły jednego z wdrożeń zostaną opisane w kolejnym numerze „Pod kontrolą”, którego wydanie planujemy na początku przyszłego roku.