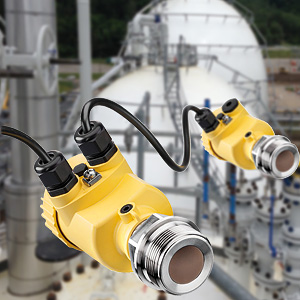
Reaktory są specyficznymi zbiornikami w całym procesie produkcji. Zachodzą w nich kluczowe reakcje chemiczne mające wpływ na wydajność, powtarzalność oraz jakość produktu końcowego. Z punktu widzenia pomiarowca jest to jedno z najtrudniejszych miejsc do przeprowadzenia jakichkolwiek pomiarów. W artykule przyjrzę się rozwiązaniom, które zostały zastosowane zarówno w Polsce, jak i przez naszych dostawców za granicą. Zgodnie z naszą filozofią działania, proponowane rozwiązania pochodzą od kilku specjalistycznych dostawców. Każdy z nich oferuje ciekawe i optymalne rozwiązanie dla pewnej, określonej grupy aplikacji. W związku z tym artykuł ten proszę traktować jako moją opinię jako członka kadry inżynierskiej firmy INTROL, a nie materiał reklamowy którejkolwiek z oferowanych firm. Proponowane rozwiązanie ułożone są według orientacyjnej ceny urządzeń, ich zalet oraz ograniczeń.
POMIAR POZIOMU W REAKTORACH – NIEŁATWE ZADANIE
Dla pomiarowca kontrola poziomu (i nie tylko) w reaktorze to naprawdę ambitne zadania.Wpływ na to ma kilka decydujących o skuteczności pomiaru czynników:
• zmienne właściwości fizyko-chemiczne produktu wewnątrz reaktora, czasami trudne do określenia,
• trudne lub czasem ekstremalne warunki pomiarowe np.: wysokie ciśnienia i temperatury,
• występowanie bardzo agresywnych substancji,
• konstrukcje przeszkadzające w pomiarze np.: mieszadła, nagrzewnice,
• ograniczona (czasem brak) możliwości przygotowania odpowiednich króćców pomiarowych, konieczność wykorzystania istniejących przyłączy.

Rysunek 1. Sonda Vegapuls 64 w reaktorze z pianą
Ostatni punkt dotyczący króćców jest często decydujący o wyborze urządzenia. Propozycja ingerencji w konstrukcję reaktora jest bowiem często „nieprzychylnie” przyjmowana z uwagi na koszty, dopuszczenia UDT, konieczność zmiany dokumentacji itp. Istotnym ograniczeniem jest również certyfikacja urządzeń, czyli konieczność posiadania odpowiednich atestów (w zależności od przemysłu): ATEX, SIL, higienicznych itp. Warto także zauważyć, że pewne rozwiązania są stosowane tylko w przypadkach krytycznych, inne są powszechne, nawet jeśli nie są optymalne.
ROZWIĄZANIE NR 1 – SONDY RADAROWE POZIOMU VEGAPULS 64
Rozwój w zakresie tej technologii na przestrzeni ostatnich dwóch dekad pozwolił na dość szerokie wykorzystanie techniki radarowej w pomiarze poziomu. W przypadku reaktorów, bardzo wygodna jest możliwość bezkontaktowego mierzenia poziomu z króćca umieszczonego w dachu zbiornika. Istotną rewolucją jest technologia 80 GHz reprezentowana przez sondę VEGAPULS 64.

Rysunek 2. Schemat montażu Vegapuls 64
Zmianą w stosunku do technologii 26 GHz jest bardzo wąska wiązka pomiarowa i miniaturyzacja urządzenia. Sonda pozwala na pomiar przez króćce od G¾ (małe reaktory), choć optymalny jest króciec od DN 50. Co istotne, sondy mogą zostać zainstalowane w dość wysokich kominach np.: o wysokości nawet 500 mm, co często ma miejsce z uwagi na bogate ”obłożenie” dachu zbiornika lub obawą przez zachlapaniem anteny podczas mieszania. Dodatkowo, pojawiła się możliwość montażu sondy na zaworze kulowym – idealne rozwiązanie umożliwiające wymianę czujnika poziomu lub kontrolę membrany anteny, praktycznie w dowolnym momencie procesu. Sonda radarowa VEGAPULS 64 dostępna jest z płaską anteną wykonaną w całości z PTFE oraz bardzo czułym nadajnikiem, który pozwala na pomiar przy ciągłej kondesacji pary wodnej na antenie. Od razu chciałem zastrzec, że jest to cecha sondy VEGAPULS 64, a nie całej serii urządzeń. Sonda ma całkowicie inną konstrukcję niż ekonomiczne odpowiedniki do gospodarki wod-kan czy zbiorników magazynowych. W praktyce oznacza to, że radarowy czujnik poziomu VEGAPULS 64 cechuje się znacznie lepszym stosunkiem sygnału do szumu, specjalnym „naddatkiem” na straty związane z oblepieniem anteny, kondesacją oraz występowaniem piany na powierzchni.

Rysunek 3. Sonda Vegapuls 64 zamontowana na dachu reaktora
Ostatni argument, czyli piana, musi być często sprawdzony w praktyce za pomocą pomiarów testowych. Pojęcie piany jest bowiem zbyt szerokie, aby jednoznacznie stwierdzić jakie jest tłumienie i rozproszenie wiązki radarowej, która propaguje wewnątrz piany. Obecne doświadczenia potwierdzają, że do około 20-30 cm piany sonda działa niezawodnie. Występowanie mieszadeł nie stanowi poważnego problemu, jeśli sonda jest zainstalowana w odpowiednim miejscu oraz zostanie „nauczona” fałszywych ech od ramion mieszadła. Miejsce montażu sondy jest czynnikiem krytycznym przy zastosowaniu radaru – montaż bezpośrednio nad np.: nagrzewnicami uniemożliwia detekcję prawidłowego poziomu. Ciekawym rozwiązaniem jest zastosowanie sondy o częstotliwości 26 GHz w połączeniu z rurą pomiarową, której geometryczne wymiary można dość dowolnie kształtować. Tego typu pomiar służy głównie do utrzymania poziomu podczas procesu w interesującym technologa zakresie i pozwala na obejście problemu braku odpowiedniego króćca. Należy zauważyć, że nie stosujemy rur pomiarowych w przypadku sond 80 Ghz.
Występowanie mieszadeł nie stanowi poważnego problemu, jeśli sonda jest zainstalowana w odpowiednim miejscu oraz zostanie „nauczona” fałszywych ech od ramion mieszadła.
Ograniczenia dotyczące sond radarowych dotyczą następujących przypadków:
• brak odpowiednich króćców na dachu lub nieodpowiednie ich umieszczenia np.: dokładnie nad elementami zakłócającymi pomiar,
• występowanie wysokiego poziomu piany,
• silna krystalizacja produktu na ścianach zbiornika, w tym na antenie radaru (brak możliwości przedmuchu),
• ciśnienie powyżej 40 bar lub/i temperatura powyżej 200°C. Co prawda istnieją sondy o dopuszczalnej temperaturze +450°C i ciśnieniu do 160 bar o częstotliwości 26 GHz z uszczelnieniem ceramicznym, lecz ich zastosowanie w reaktorach jest ograniczone z uwagi na trochę mniejszą moc wiązki oraz przyłącza od DN 150.

Rysunek 4. Schemat montażu sondy radarowej z rurą pomiarową
Chciałbym również zasygnalizować, że w przypadku kalibracji sond na reaktorach, należy wziąć pod uwagę wizytę naszego serwisanta, który ma minimum kilkuletnie doświadczenie na tego typu urządzeniach. Funkcjonalność „plug and play” działa rewelacyjnie na standardowych rozwiązaniach, takich jak zbiorniki magazynowe czy proste aplikacje. Trzeba jednak pamiętać, że nadal funkcjonują parametry specjalne dla wyjątkowo ciężkich aplikacji, a reaktory bez wątpienia należą do tej kategorii. W wyjątkowo trudnych przypadkach najlepszą metodą rozwiązania problemów jest zarejestrowanie echa przez kilka dni i jego analiza.
W większości przypadków, po zmianie kilku parametrów specjalnych, możemy cieszyć się prawidłową praca sondy przez kolejne dekady.

Rysunek 6. Schemat pomiaru różnicy ciśnień
ROZWIĄZANIE NR 2 – POMIAR RÓŻNICY CIŚNIEŃ FUJI LUB CIŚNIENIA VEGABAR
Jest to jedna z najstarszych metod pomiaru poziomu, polegająca na pomiarze różnicy ciśnień wewnątrz reaktora. Jedna sonda instalowana jest blisko dna, druga powyżej górnego poziomu cieczy. W chwili obecnej mamy do wyboru 2 rozwiązania:
pierwsze – klasyczne, z przetwornikiem różnicy ciśnień FUJI wyposażonym w kapilary oraz separatory membranowe z bogatą ofertą materiałów o bardzo wysokiej odporności chemicznej. Rozwiązanie jest bardzo pewne z wyjątkiem problemów z wpływem zmian temperatury otoczenia na ciecz wypełniającą kapilary. Typowym błędem ze strony użytkownika jest pomijanie wpływu zastosowania separatorów, przy obliczeniach całkowitej niepewności pomiaru.

Rysunek 5. Przetwornik różnicy ciśnień Fuji FKC
Drugim rozwiązaniem jest zastosowanie dwóch przetworników ciśnienia VEGABAR (jeden posiada specjalną elektronikę), które w sposób elektroniczny odejmują od pomiaru całkowitego wartość ciśnienia statycznego nad cieczą. W tym przypadku bardzo upraszczamy montaż urządzenia, nie potrzebujemy kapilar, a tylko zwykłe przewody sygnałowe. Należy jednak pamiętać, że rozwiązanie to jest teoretycznie znacznie mniej dokładne niż zastosowanie przetwornika różnicy ciśnień. Co niemniej ważne, może być ono stosowane wyłącznie, jeśli ciśnienie statyczne nie jest większe niż 8-krotność ciśnienia hydrostatycznego wywołanego maksymalnym poziomem cieczy (np.: dla reaktora o wysokości 10 m max ciśnienie statyczne może wynosić 8 bar).

Rysunek 7. Przetworniki: Primary i Secondary
Pomiary różnicy ciśnień są bardzo łatwe w kalibracji oraz rozwiązują problem braku przyłączy w dachu zbiornika.
Przetworniki różnicy ciśnień są bardzo łatwe w kalibracji oraz rozwiązują problem braku przyłączy w dachu zbiornika. Kolejnymi zaletami jest brak wpływu instalacji wewnętrznych oraz występowania piany. FUJI produkuje przetworniki dla zakresu ciśnienia statycznego nawet powyżej 1000 bar, maksymalnej temperaturze procesu
400oC, a nawet wersje specjalne z dopuszczeniem do pomiaru mediów radioaktywnych. Niedogodnością natomiast jest wpływ zmian gęstości medium, która wpływa 1:1 dla dokładności pomiaru. Potrzebne są również 2 króćce pomiarowe, co czasami jest problemem na działających aplikacjach.
Istotną informacją jest możliwość zamówienia sond VEGA z przyłączami gwintowanymi i membranami czołowymi wraz ze specjalnym zaworem kulowym, który umożliwia demontaż sondy w czasie procesu. Armatura ma bardzo ciekawą konstrukcję, która zapewnia zlicowanie membrany sondy ze ścianą zbiornika. Nie jest to jednak tak tanie rozwiązanie, jak w przypadku sony radarowej ze zwykłym zaworem kulowym.
ROZWIĄZANIE NR 3 – POMIARY IZOTOPOWE BERTHOLD TECHNOLOGIES
Zdaję sobie sprawę, że na słowo „izotopowy” nie raz kończyła się rozmowa z klientem na temat pomiaru poziomu w ekstremalnych aplikacjach. Konieczność posiadania zezwolenia prezesa Państwowej Agencji Atomistyki, posiadanie inspektora ochrony radiologicznej, kontrola szczelności źródeł, plus obowiązkowa biurokracja spędzają sen z oczu niejednemu kierownikowi działu AKPiA. Z drugiej strony, każdego miesiąca instalujemy lub serwisujemy tego typu systemy w Polsce. Praktycznie od początku naszej działalności posiadamy wszelkie uprawnienia, magazyn izotopów, umowę na odbiór i utylizację starych źródeł, doświadczenie w imporcie źródeł, czy inspektora ochrony radiologicznej. Pomiar izotopowy nie jest więc dla nas czymś nowym, a w pewnych sytuacjach jest jedyną skuteczną metodą. Pomiar izotopowy składa się z 2 elementów: źródła promieniowania (kobalt lub cez) oraz detektora.

Rysunek 8. Schemat działania układu izotopowego LB440
Oba elementy układu znajdują się na zewnątrz reaktora, w związku z tym nie interesuje nas dostępność króćców, temperatury i ciśnienia wewnątrz reaktora, agresywność medium itd. W jednej z naszych najtrudniejszych aplikacji pomiar działa na reaktorze o grubości ściany prawie 200 mm. Samo źródło umieszczone jest w specjalnej, grubościennej pochwie wewnątrz zbiornika. Przy odpowiednim dobraniu źródła, urządzenie jest bezobsługowe nawet przez dekadę.
Obecnie aktywność źródeł izotopowych jest znacznie niższa niż w przeszłości.
Detektory liniowe firmy Berthold z kryształami wykorzystujące scyntylacje (rozbłyski światła, które wykrywane są przez fotopowielacze) są w chwili obecnej nawet 10 razy czulsze od tradycyjnych komór jonizacyjnych. W związku z tym również aktywność źródeł jest znacznie niższa niż w przeszłości. Odpowiednie rozmieszczenie układów źródło – odbiornik pozwala na pomiar całego parku reaktorów w niedużej odległości od siebie. Praktycznie każdy zakład chemiczny czy rafineria w Polsce posiada rozwiązania od firmy Berthold. Koszt takiego rozwiązania może wydawać się dość spory. Biorąc jednak pod uwagę koszty utrzymania pomiaru przez 2 dekady, spodziewane problemy z pomiarami kontaktowymi, bezobsługowość czyli redukcję obowiązków działu utrzymania ruchu, wielu klientów określa pomiar izotopowy jako optymalne, ekonomicznie i bezobsługowe rozwiązanie.

Rysunek 9. Kamera wizyjna Canty w reaktorze
ROZWIĄZANIE NR 4 – SYSTEMY WIZYJNE FIRMY CANTY
Jest to ciekawy i nowatorski system polegający na zastosowaniu kamery wizyjnej ze zintegrowanym oświetleniem wnętrza zbiornika.
System ma w standardzie 4 funkcjonalności:
• podgląd wizyjny procesu dla operatora,
• pomiar poziomu w zbiorniku,
• pomiar ilości piany na powierzchni cieczy,
• wykrywanie całkowitego opróżnienia zbiornika.
Pomiar poziomu opiera się na wykrywaniu punktu na ścianie reaktora, w którym następuje zmiana kontrastu pomiędzy medium w zbiorniku, a wolną ścianą reaktora. W odróżnieniu od sond radarowych, nie musimy się przejmować instalacjami wewnętrznymi. Musimy jedynie umieścić kamerę tak, aby optyka widziała ścianę na całym wymaganym zakresie zmian pomiaru poziomu. Co istotne, jest to pomiar poziomu tylko górnej warstwy medium, bez względu czy jest to jeszcze ciecz czy piana. Dodatkowe wyjście pozwala na określenie ile procent powierzchni jest pokryte pianą, co jest idealne do kontroli procesu np.: fermentacji czy dodawania środków antypieniących. Można również wykryć, czy nastąpiło całkowite opróżnienie reaktora, zarówno po opróżnieniu zbiornika z podstawowego produktu, jak i środka czyszczącego między kolejnymi procesami. Nasza czeska firma INTROL Automation s.r.o. jest w trakcie realizacji pierwszego projektu w 40 letnim reaktorze o grubości ściany 80 mm. Należy dodać, że w dostawie jest kamera ze zintegrowanym układem przemywania optyki wodą (okno wziernikowe jest częścią optyki), wewnętrznym oświetleniem zbiornika, układem chłodzenia elektroniki kamery sprężonym powietrzem oraz zewnętrznym modułem do pomiaru poziomu i piany.
Wszystkie te elementy posiadają atesty do pracy w strefie zagrożenia wybuchem.
POMIAR POZIOMU W REAKTORZE – WIELE ROZWIĄZAŃ OD INTROLU
Poziom w reaktorach można mierzyć na kilka różnych sposobów. Należy jednak brać pod uwagę wiele czynników związanych między innymi z właściwościami mierzonego medium, konstrukcją reaktora, możliwościami ingerencji w ściany reaktora oraz oczywiście budżetem. Nasza współpraca z różnymi dostawcami daje nam szerokie portfolio rozwiązań dla trudnych i często nieszablonowych pomiarów poziomu. Dla każdego z oferowanych układów posiadamy kadrę inżynierską przeszkoloną bezpośrednio przez naszych dostawców. Nasi inżynierowie mają kompetencje i wieloletnie doświadczenie w uruchomieniach takich systemów i ich serwisowaniu. Dodatkowo we współpracy z innymi firmami z Grupy Introl możemy zaoferować pełne wykonanie projektu, od prostego montażu sond radarowych, po dostawy, montaż i serwisowanie urządzeń izotopowych.