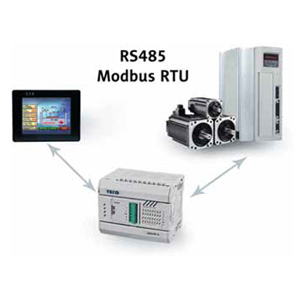
Wizytując polskie obiekty przemysłowe, obok nowoczesnych systemów pełnych złożonych układów automatyki, nie sposób nie dostrzec także starych, wysłużonych maszyn, których data produkcji to nawet połowa zeszłego stulecia. Co z pozoru może okazać się dziwne, ich wiek często nie idzie w parze ze stanem mechnicznym, a mające kilkadziesiąt lat urządzenia cechuje jeszcze bardzo wysoka sprawność i niezawodność. Jedynym problem jest brak automatyki, której po prostu nie było w okresie wyprodukowania danej maszyny. W takich sytuacjach zakup nowych, kosztownych maszyn, wyposażonych w rozbudowane funkcje komunikacji i automatyzacji pracy, jest często zabiegiem zbędnym. Zupełnie wystarczającą staje się natomiast modernizacja tego co już mamy.
Nieprogramowalna nawijarka transformatorowa
Rosnące zapotrzebowanie na energię elektryczną jest głównym czynnikiem wzrostu rynku transformatorów. O pozyskaniu kontrahenta decyduje czas realizacji zamówienia oraz cena. Przyjęło się, że okres wykonania takiego urządzenia to około 3-4 tygodni, a producenci aby być bardziej konkurencyjnym, dążą do ciągłego skracania terminów realizacji. Ta presja czasu i kosztów powoduje, że proces produkcji musi być optymalizowany, a tutaj niezawodna okazuje się automatyka. Z chęcią modernizacji swoich maszyn zwrócił się do nas Klient działający w branży elektroenergetycznej; rozpoczynający produkcję transformatorów żywicznych. Klient posiadał dość przestarzałe – pod względem automatyki – nawijarki transformatorowe. W wyniku oględzin jednej z maszyn, zapadła decyzja o jej częściowej modernizacji, a zadecydowały o tym względy ekonomiczne. Jak się bowiem okazało, część mechaniczna maszyny pochodzącej z lat 70. poprzedniego stulecia, była w bardzo dobrym stanie. Wymiany na nowsze i bardziej niezawodne wymagały natomiast układy odpowiadające za dokładne układanie izolacji. Najważniejsza rzecz, która musiała zostać wykonana (a niedostępna przeszło 40 lat temu) to wprowadzenie możliwości programowania maszyny przez operatora.
Trafiona propozycja
W wyniku analizy całego procesu i uwarunkowań technologicznych, zaproponowane zostało rozwiązania bazujące na serwonapędzie i współpracującym z nim sterowniku PLC. Po wykonanej modernizacji, cała maszyna składa się z trzech elementów:
- bębna, na który nawijane są warstwy izolacji i drutu (niemodernizowana część mechaniczna)
- serwonapędu połączonego ze „stołem” za pomocą przekładni ślimakowej,
- sterownika PLC współpracującego z układem nadzorującym pracę serwonapędu.
Napęd bębna stanowi silnik prądu stałego wraz z regulatorem, pochodzące jeszcze ze starej maszyny (ciągle sprawne elementy), sterownik programowalny TECO TP03-30HR-A z modułem analogowym TP03-3MA oraz serwozasilacz TECO JSDA-75A3 współpracujący z serwonapędem TECO JSMAMC30ABK.
Dodatkowy element stanowi panel operatorski Weintek, umożliwiający wprowadzanie danych do programu, jak również jego nadzór podczas pracy maszyny. Zarówno sterownik PLC, jak i serwozasilacz oraz panel operatorski, wyposażone są w porty komunikacyjne RS485, pozwalające na przesyłanie danych pomiędzy urządzeniami za pomocą protokołu Modbus RTU.
Zasada działania
Zadaniem maszyny jest nawijanie kolejnych warstw izolacji lub drutu w taki sposób, aby kolejne zwoje znajdowały się jeden za drugim (Rys. 2). Aby nawijanie było możliwe, potrzebna jest współpraca dwóch elementów szablonu – bębna oraz stołu (Rys. 1).

Rys. 1: Ruchome elementy maszyny

Rys. 2: Nawijanie izolacji „zwój przy zwoju”

Rys. 3: Izolacja krzyżowa
Szablon obraca się wokół własnej osi dając efekt nawijania, a stół rozmieszcza kolejne zwoje izolacji na bębnie.
Innym przypadkiem jest nawijanie izolacji rovingowej – krzyżowej tzn. zwoje nawijane są w znacznej odległości od siebie tworząc wzór krzyża na szablonie (Rys. 3). Ten typ izolacji można porównać do szpuli nici, którą nawija się najpierw w jednym kierunku, następnie w drugim, a przecinające się nitki układają się w kształcie krzyża.
Nawijarka posiada trzy tryby pracy: automatyczny, nożny oraz swobodny. W trybie automatycznym program jest realizowany linijka po linijce, zgodnie z prędkością zadaną przez operatora (z potencjometru) oraz kierunkiem nawijania. Maszyna automatycznie wyznacza punkt startu, końca oraz długość niezbędną do nawinięcia izolacji lub drutu. Z kolei w trybie nożnym operator nastawia prędkość za pomocą przycisku nożnego. Tryb ten, w odróżnieniu od trybu automatycznego, nie realizuje programu linijka po linijce, lecz niezbędna jest obecność operatora w celu zatwierdzenia przejścia do następnej linijki programu. W trybie swobodnym, nawijana cewka obraca się w pożądanym kierunku, jednak bez posuwu stołu. Konieczność zastosowania tego trybu występuje zwłaszcza przy tzw. odczepach, kiedy operator musi odciąć drut dochodzący do szablonu i zablokować w ten sposób posuw stołu, jednocześnie nie blokując obrotu wrzeciona. Dzięki takiemu działaniu, żywica pokrywająca szablon nie ocieka i nie dochodzi do spowodowania zanieczyszczeń lub zgrubienia w szablonie.
Innowacyjne rozwiązania
W trakcie prac nad modernizacja nawijarki zdecydowaliśmy się na innowacyjne rozwiązana polegające na zastosowaniu tzw. „receptur” w panelu operatorskim Weintek oraz wykorzystaniu trybu pracy „Position/Speed mode” w serwonapędzie.
Wykorzystanie tzw. „receptur” ma szczególne znaczenie dla procesu wprowadzania danych do systemu sterownia. Wszystkie dane standardowo mogą być wprowadzone na dwa sposoby. W pierwszym z nich użytkownik samodzielnie wprowadza dane do panelu operatorskiego na kilku ekranach HMI. Niektóre informacje odnoszą się stricte do procesu nawijania transformatora, inne z kolei pełnią rolę informacyjną dla pracowników obsługujących urządzenie. Zaletą wprowadzania danych tym sposobem jest niewątpliwie możliwość wizualnej oceny poprawności wpisywanych informacji, które na ekranie panelu wyświetlają się w postaci graficznej (Rys. 4).

Rys. 4: Wprowadzanie danych za pomocą ekranu w HMI
Istotną wadę stanowi natomiast czasochłonność, ponieważ operator musi wprowadzić każdą linijkę programu (a przeciętnie występuje ich ok. 250), bez możliwości kopiowania powtarzających się linijek (receptury). Niemal dokładnie odwrotna sytuacja ma miejsce przy posługiwaniu się drugim sposobem – przygotowanie danych w plikach „Microsoft Excel” bądź „OpenOffice Calc” (Rys. 5).

Rys. 5: Wprowadzenie danych za pomocą programu OpenOffice Calc
Korzystanie z popularnych arkuszy kalkulacyjnych pozwala na znaczną oszczędność czasu. Wadą tej metody jest jednak brak graficznej ilustracji danych. Wobec wad i zalet obu metod, idealnym dla użytkownika wydaje się być rozwiązanie kompromisowe, czyli wprowadzenie danych na komputerze PC, a weryfikacja ich poprawności na graficznym interfejsie (Rys. 6).

Rys. 6: Podgląd aktualnie wykonywanej linijki programu.
Takie też rozwiązanie zastosowaliśmy, dzięki czemu uprzednio wprowadzone do arkuszy kalkulacyjnych dane, przenoszone są z komputera PC do panelu, za pomocą nośników informacji w postaci pendrive’a bądź kart CF. Wspomnianymi danymi są wartości takie jak: drut/izolacja, punkt startu w milimetrach, wymiar drutu/szerokość izolacji, liczba zwojów/szerokość izolacji, kierunek nawijania, dowijanie zwojów.
Drugim zastosowanym rozwiązaniem jest użycie trybu „Position/Speed mode”, czyli naśladowanie ruchu wrzeciona przez serwonapęd, przy wykorzystaniu elektronicznej przekładni obrotów serwo (electronic ear ratio). Aby wytłumaczyć pokrótce zasadę działania wymienionej przekładni, załóżmy sytuację, w której na jeden obrót wrzeciona przypada jeden obrót serwo, co powoduje posuw stołu o 3 mm (wartość stała). Posuw stołu ściśle zależy od szerokości izolacji – jeżeli izolacja ma wymiar 35 mm, stół musi się przesunąć o taką samą odległość.

Rys. 7: Schemat wymiany danych pomiędzy urządzeniami
Szerokość izolacji nawijanej na szablon jest jednak zmienna i mieści się w zakresie od 6 mm (dwa obroty serwo na obrót bębna) do 225 mm (75 obrotów serwo na obrót bębna). Zachodzi więc potrzeba regulacji ilości obrotów serwo, przypadających na jeden obrót bębna i właśnie do tego celu służy elektroniczna przekładnia obrotów serwo. Dane o szerokości izolacji pobierane są z panelu operatorskiego, przetwarzane przez sterownik, a następnie wysyłane do serwo.
Proste programowanie
Do oprogramowania panelu Weinteka wykorzystano oprogramowanie EasyBuilder 8000 v3.01 dostarczone przez producenta HMI. W celu konwersji plików Excel i OpenOffice na postać zrozumiałą dla panelu, użyto funkcji „Recipe/Extended Memory Editor”. Niezastąpionym narzędziem okazała się wbudowana funkcja Macro, w której możemy napisać praktycznie dowolny skrypt, pomocny przy przeliczaniu jednostek. Pomimo tego, że soft jest zupełnie darmowy, jego funkcjonalność i niezawodność znacznie przewyższają niektóre płatne oprogramowania. Program na sterownik PLC został wykonany w środowisku drabinkowym LAD, za pomocą oprogramowania TP3-PCLink, dostarczonego przez producenta sterownika. Wbudowany w urządzeniach protokół Modbus RTU znacznie ułatwił i przyspieszył wymianę danych, a standard RS485 okazał się niezastąpiony w środowisku, w którym występują zakłócenia.
Optymalne dopasowanie
W modernizacji nawijarki transformatorowej, połączenie nowoczesnego systemu sterowania, opartego na serwomechanizmie ze sterownikiem programowalnym TECO, okazało się strzałem w dziesiątkę. System świetnie spisuje się we współpracy z nieco starszymi elementami mechanicznymi takimi jak stół, bęben i przekładnia. Dzięki częściowej modernizacji posiadanej nawijarki, Klient zautomatyzował proces, przy relatywnie niskich kosztach (nieporównywalnych z zakupem nowego systemu automatycznego nawijania). Dalsza modernizacja maszyny będzie zmierzać w kierunku wymiany silnika prądu stałego z regulatorem, na silnik prądu zmiennego z falownikiem. Zredukuje to powstające zakłócenia. Opisana w artykule modernizacja jest tylko przykładem takich przemyślanych inwestycji, realizowanych dla naszych Klientów z przeróżnych branż. Często bowiem, zamiast inwestować ogromne pieniądze w nowe maszyny, wystarczy poszukać rozwiązań alternatywnych, pozwalających na optymalizacje procesów przy zdecydowanie mniejszych nakładach finansowych.